1 chin 14 ounces of sulfur, together with 2 1/2 chin of saltpeter, 5 ounces of charcoal, 2 1/2 ounces of pitch, and 2 1/2 ounces of dried varnish are powdered and mixed. Next, 2 ounces of dried plant material, 5 ounces of tung oil, and 2 1/2 ounces of wax are also mixed to form a paste. Then these ingredients are all mixed together, and slowly stirred, The mixture is then wrapped in a parcel with five layers of paper, which is fastened with hempen thread, and some melted pitch and wax and is put on the surface.
It was in the early thirteenth century that man turned toy fireworks into weapons of war. The first recorded use of rockets as military weapons was in defense of Kai Fung Fu, China, in 1232. The Chinese "arrows of fire" were fired from a sort of crude rack-type launcher. The black powder was packed in a closed tube (probably bamboo) that had a hole in one end for the escaping hot gases, and a long stick as an elementary guidance (or stabilization) system.
Black powder had a very low specific impulse. About 1280 AD, Arab military men, referring to the propulsive ability of black powder, suggested improvements over the simple Chinese skyrocket. One interesting innovation was what might be best described as an air squid or travelling land mine; it could scurry across land in the manner of a squid through water.
By about 1400 when rocketry became of commercial importance throughout Europe and especially in Italy- where perhaps the greatest designers of pyrotechnics were found. The use of fireworks for all sorts of celebrations created a major market for the manufacture of large quantities of rockets. This spread throughout Europe and reached its zenith during the middle of the eighteenth century.
One of the earliest technical publication on rocketry, the Treatise Upon Several Kinds of War-Fireworks, appeared in France in 1561. The treatise made a critical analysis of the rockets used in earlier military campaigns. A recommendation was made to substitute varnished leather cases for the commonly accepted paper and bamboo ones. There is no evidence that this suggestion was followed by later rocketeers.
Refinements in rocket design came faster over the next few hundred years, at least on paper. In 1591, some three hundred years before Goddard, a Belgian, Jean Beavie, described and sketched the important idea of multistage rockets. Multistaging, placing two or more pockets in line and firing them in step fashion, is the practical answer to the problem of escaping earth's gravitational attraction. An even earlier forerunner was Conrad Haas, chief of the artillery arsenal in Sibiu, Romania, between 1529 and 1569.
By 1600, rockets were being used in various parts of Europe against cavalry, foreshadowing the modern antitank hand weapon, the bazooka of World War II and Korean fame. Later, in 1630, a paper was written describing exploding aerial rockets which created an effect similar to that of the twentieth-century shrapnel shell. By 1688, rockets weighing over 120 pounds had been built and fired with success in Germany. These German rockets, carrying 16- pound warheads, used wooden powder cases reinforced with linen.
Toward the end of the eighteenth century a London lawyer, Sir William Congreve, became fascinated by the challenge of improving rockets. He made extensive experimentation with propellants and case design. His systematic approach to the problem resulted in improved range, guidance (stabilization), and incendiary capabilities. The British armed forces used Congreve's new rockets to great advantage during the Napoleonic Wars.
When Congreve died in 1828, his applied engineering and dedication had already resulted in several technological advances. In addition to fortified cases, new propellants, and incendiaries, Congreve developed stabilizing fins that provided rocketeer with effective stabilised rockets. Congreve rockets were built in weights of 18, 24, 32, 42, 100, and 300 pounds (8, 11, 15, 19, 45, and 136 kg).
In 1906, Alfred Maul successfully took aerial photographs by attaching a camera to a black powder rocket (thereby creating the first instrumented sounding rocket).
During World War I, Le Prieur black powder rockets were sometimes fired from French and British biplanes or from the ground against German captive balloons. Otherwise, military rockets could not compete in range or accuracy with artillery of the day.
In United States, beginning in 1915, many tests were conducted, by Goddard, with rockets using black powder.
In early June 1927, rocket and space enthusiasts in Germany founded the Verein fuer Raumschiffahrt (Society for Space Travel). Some members experimented with black powder rockets.
Automobile manufacturer Fritz von Opel piloted his own rocket glider, Opel Rak.2, in tests near Frankfurt on 30 September 1928. Its 16 rockets, each producing 50 pounds of thrust, were build by Friedrich Sander a pyrotechnics specialist. The propulsion system combining high-thrust, fast-burning powder rockets for initial acceleration with lower-thrust, slower-burning rockets to sustain velocity.
Opel approached Alexander M. Lippisch, a young designer working at the Rhon-Rossitten-Gesellschaft, who had already displayed a penchant for the unorthodox in airplane configuration, with the proposal that he, too, design a glider for rocket power.
Max Valier and Alexander Sander also succeeded in arousing enthusiasm for rocket propulsion in a twenty- seven-year-old aircraft designer, Gottlop Espenlaub. His E 15 tail-less design was of interest as a rocketplane.
On 11 June, Fritz Stamer effected the first rocket- propelled flight in Lippisch's glider. The glider had been dubbed Ente, or Duck. That lead later to the Lippisch's Komet - the Messerschmitt Me 163, liquid rocket manned interceptor.
Reinhold Tiling launched a black-powder rocket from Osnabruck in 1931. It rose to a height of 2.5 miles.
Gerhard Zucker envisioned rocket mail service across the English Channel. The longest shot he attempted was from Harris to Scarp, in western Scotland, on 31 July 1934. But the rocket blew up before takeoff.
In 1939 researchers at the California Institute of Technology in California, seeking to develop a high performance solid rocket motor to assist aircraft takeoff, combined black powder with common road asphalt to produce the first true composite motor. This was the birth of the true composite motor and marked the end of the use of black powder in major rocketry applications.
Double-base solid propellant
Double-base solid propellants consist mainly of fibrous nitro-cellulose and a gelatinizer, or plasticizer, such as nitroglycerine or a similar compound (ethylene glycol dinitrate), each containing oxygen and fuel in the same compound. The term double-base originated from the application of these mixtures as gun propellants. They contained two active constituents, and this name distinguished them from the "single base" smokeless powders which utilized either nitro-cellulose (gun cotton) or nitroglycerine singly as the active constituent.
The first double-base propellant was made by Alfred Nobel in 1888, and was used as a smokeless powder. In such propellants, a high nitroglycerine content tends to increase the energy and burning rate; a high nitro-cellulose content helps to impart a strength to the propellant. The first experiments with double-base smokeless powders as rocket propellant seem to have been made by Goddard in 1918 and by F W Sander in Germany around 1935. The results did not appear to be very promising.
Walter Dornberger, Chief of German rocketry reported: "In 1930.... I got the order to make military weapons out of solid rockets, using, if possible, smokeless powder. This was to be accomplished in military facilities... These solid rocket weapons were ready for mass production as early as 1934".
In Russia, N I Tikhomirov and I P Grave independently proposed to use smokeless powder in rockets before World War I, but these proposals received no official support. After 1917 the attitude changed sharply. Even during the Civil War, engineers N I Tikhomirov and V A Artemev started work on the design of smokeless powder rocket and in 1921 a special laboratory was set up for these studies in Moscow. They became convinced of the necessity of creating a special, slow-burning rocket powder. In 1924, O.G. Filipov and S.A. Serikov, pyrotechnic specialists working at the Artillery Academy then located in Leningrad, developed a formula for a new type of powder based on a non-volatile solvent: 76.5% by weight of nitro-cellulose, 23% TNT, and 0.5% centralite to retard burning. It was called "PTP", i.e. Pyroxyline TNT Powder. By 1928-29, the work conducted in the Artillery Academy permitted development of a semi-production technique for preparing the PTP. A rocket was designed using these solid charges and it was successfully tested on March 3, 1928. In 1929 the basic 24mm solid charges made from PTP, which were prepared in the laboratory shops in great quantities, were selected as the standard in Gas Dynamics Laboratory, the new formed GDL. Therefore, on this standard engineers developed three basic sizes of scaled-up rocket chambers of 68, 82, and 132mm caliber. The latter two subsequently became the basic caliber of Soviet rockets for decades: the RS-82 and the RS-132, later named "Katyusha". An 82mm Jet-Assisted Takeoff rocket was flight tested on the Y-1 and TB-1 aircraft in 1932-33.
In the USSR after World War II, 0.5 ton, 300-400mm rocket motor charges of double-base ballistite were produced for various rockets and missiles. In 1959 the NII-125 (now NPO Soyuz of Liouberetsky) suggested to build ballistite charges of 4 to 5 tons, 1 meter in diameter and 5 to 6 meters long. Korolev then begin to study the RT-1/8K95 predecessor of the RT-2/8K98 ICBM (alias SS-13 Savage) with 4 X 800mm charges of ballistite as the first stage. The fiberglass cluster produced 100 tons of thrust for 30 seconds. But flight tests of the RT-1 from April 1962 to June 1963 at Kapustin Yar were not very successful. The project was cancelled.
In Great Britain, in December 1934 Alvyn Douglas Crow, Director of Ballistic Research at the Woolwich Royal Arsenal, proposed to Sir Hugh Elles, Master of General Ordnance, that the British begin to investigate the possibilities of developing rocket weapons powered by smokeless cordite powder of the unrestricted burning type. Work began in May 1935 and by the summer of 1936 encouraging advances in technique had been achieved. Ultimately Crow headed Britain' wartime rocket program.
In the United States, Parsons and Forman of GALCIT (Guggenheim Aeronautical Laboratory, California Institute of Technology) in 1938 built and tested a smokeless powder constant-volume combustion motor similar to the one that had been used by Goddard. They concluded after these tests that the mechanical complications of constructing an engine using successive impulses to obtain thrust duration of over 10 seconds was impractical. During 1939 and 1940, various mixtures of smokeless powder with black powder (the first double-base/composite propellant) were tested. Most of the tests ended in an explosion. There were those who were convinced that the combustion process of a restricted burning charge in a rocket motor was basically unstable.
In 1917-1918, while studying for his master's degree under A.G. Webster at Clark University, Clarence N. Hickman had met Goddard. Acting upon the suggestion of L.T.E. Thompson, Webster's assistant, Goddard sought Hickman's aid in solving some mechanical problems, with the result that the two worked together during World War I in California, and later at the Aberdeen Proving Ground in Maryland (where Goddard developed a prototype of the Bazooka). After the war Goddard, Thompson, and Hickman continued their association (1920-23). During World War II, the United States rocket program was under the direction of Division A (later 3) of the National Defense Research Committee, a coordinating agency established by President Franklin D. Roosevelt on 27 June 1940. By that time, Thompson was in charge of research at the Navy's Dahlgren Proving Ground, so it was rather easily arranged for Hickman's Section H to begin its testing program at that Virginia site (Section H was named for Hickman, who's letter urging a rocket development program had been instrumental in it being approved).
Because of it very little experience in high-energy solid (double-base) propellants of the type needed for extended-range, high-speed weapons, the United States drew on British rocket knowledge. Within a few years, suitable solid propellants were being produced at the Army's Radford Ordnance Works, the Navy's Indian Head Powder Factory, and the Sunflower Ordnance Works, operated by the Hercules Powder Company. Later, the Section H group moved to the Allegheny Ballistics Laboratory at nearby Pinto, West Virginia, where they worked closely with Army Ordnance, the Chemical Warfare Service, and the Air Corps. Various double-base rockets were produced during World War II including bazooka rockets, 4.5 inch, 5 inch, and 7.2 inch rockets, and the large air-launched Tiny Tim. The Tiny Tim was 11.75 inches in diameter and was later utilized as the booster for the Wac Corporal research rocket (ancestor of Aerobee and Corporal, the first big all-American liquid rocket, guided ballistic missile).
After World War II, Hercules Powder and Allegheny Ballistics Laboratory began the development of a more powerful double-base rocket. On August 20, 1947, the JATO X-201, the first 16 inch. solid-propellant booster, was flight-tested at the Naval Ordnance Test Station, Inyokern, California. The X-201 was used as well in the Naval Ordnance Bureau's Bumblebee program. The cast-double-base propellant booster, later designated the 3DS47000, was developed by Hercules Powder Company. It contained 740 lb. of propellant and delivered a thrust of about 50,000 lb. for 3 sec. It was the forerunner of an entire family of related propulsion units that served as boosters for the Nike, Terrier, Talos, and Honest John missiles.
The Bumblebee program lead directly to the Navy's Terrier and Talos missiles as follow-ons of the Lark anti-aircraft research missile. The Army's Nike-Ajax was a kind of large, guided Wac Corporal, using the same propulsion formula, but with a Bell liquid pressure feed rocket main engine. Bell later developed the pump feed rocket engine XLR65-BA-1 for the X-9 Shrike, predecessor of the Rascal air-to-ground missile. Yet another derivative was a simpler engine for a rocket-propelled pod for the B-58 Hustler bomber. The rocket pod was cancelled, but the Hustler became the basic Agena engine used on upper stages of the Thor, Atlas and Titan boosters. Bell was later involved in the ascent engine development for the Apollo lunar module.
Talos and Honest John motors were used on the big three and four stage Black Brant XI and XII NASA sounding rockets with composite upper stages. The Honest John motor was know as Taurus when used on sounding rockets.
Major later Hercules developments included the Vanguard satellite launcher third stage in the mid-1950's. Hercules developed composite/double-base high energy propellants for Minuteman, Polaris and Poseidon upper stages. (the propellant of Minuteman I third stage consisted of nitro-cellulose + nitroglycerine + triacetin + nitrodiphenylamine ammonium perchlorate + aluminum). Even higher energy propellants, with the addition of nitramine (HMX), were developed for the Trident and MX missiles.
Hercules Powder is today Alliant Techsystems and builds composite boosters for the Titan IVB, Delta II, Delta III, and the future Delta IV; all stages for Pegasus; and upper stages for the Taurus space launchers. Hercules was a pioneer in the development of fiber-wound light motor cases for Minuteman and Polaris motors.
In the late 1950's and early 1960's, Aerojet tried to develop nitro-urethane as a double-base high energy replacement, but nitrourethane had bad mechanical properties. In the end it has proved that pure double-base propellants are better for the environment than composites, but they are explosive and have relatively low specific impulse (higher with explosive HMX-nitramine added). For safety reasons they are not suited for big space launchers.
Although most solid propellants used today are classed as composites, the double-base (homogeneous) type is still much in demand. However, the gradual increase in the number and amount of additives to the original single-phase double-base propellant has narrowed the distinction between the two classes. Initially the double-base propellant was a homogeneous solid or liquid single-phase chemical system that contained enough oxidizer to sustain combustion in the same molecule with fuel.
MAJOR HERCULES MOTORS.
----------------------------------------------------
Rocket Motor Dia Length Thrust Weight
project name inch inch lb lb
----------------------------------------------------
Bumblebee X-201 16 ---- 50,000 +740
Honest John X-202 23 197.44 90,325 3,937
Nike X-216 17.57 135.51 48,700 1,193
Deacon X-220 6.8 110 6,100 155
Improved H.J.X-244 (Improved Honest John)
Talos X-251 31.11 138 ----- 4,245
Terrier X-256 18 156.61 ----- 1,839
Altair-1 X-248 18.02 58.21 2,850 513
(Vanguard Thor-Able, Thor-Delta)
Altair-2 X-258 19.07 59.25 6,510 576
(Scout-stage 4 Thor-Delta)
Antares-1 X-254 30.12 114.68 14,000 2,292
(Scout-stage 3 )
Antares-2 X-259 30.3 113.8 21,700 2,812
(Scout-stage 3 )
Minuteman M-57A1.38 85 ------ -----
(Stage 3)
Polaris A2 X-250 54 84.25 ------ -----
(Stage 2)
Polaris A3 X-260 54 88.79 ------ 9,501
(Stage 2)
Poseidon PC3-1 74.19 187.96 ------ -----
(Stage 1, with Thiokol)
Poseidon PC3-2 74 97.265 ------ -----
(Stage 2)
Trident I (with Thiokol)
Trident II (with Thiokol)
MX (third stage)
----------------------------------------------------
===========================================================
Composition of Various Double-Base Propellants (Percent)
---------------------------------------------------------
Ingredients Extruded Russian Composite Cast
Ballistite Cordite Double-
Base
---------------------------------------------------------
nitro-cellulose 51.50 56.5 21.0 47.0
nitro-glycerine 43.00 28.0 13.0 37.7
ethyl centralite 1.00 4.5 1.0 1.0
diethyl phthalate 3.25 ---- ---- ----
dimethyl phthalate ---- ---- ---- 14.0
dinitrotoluene ---- 11.0 ---- ----
carbon black 0.20 ---- 9.0 0.3
potassium sulphate 1.25 ---- ---- ----
potassium perchlorate ---- ---- 56.0 ----
--------------------------------------------------------
Composite Solid Propellants
Solid propellants of the composite type, containing separate fuel (or reducer, chemically) and oxidizer (in a separate compound) intimately mixed, replaced the simple double-base propellants to a considerable extent, especially for large non-military motors. The organic fuel material is initially in a liquid or semi-liquid form that can set to a solid (binder). Among the earliest substances used were asphalt and various synthetic rubbers. While generally not considered as composite, black powder was in fact the oldest composite propellant. Before 1940 black powder, in common use, was nearly synonymous with the words 'rocket motor' .
While working on the theory of rocket propulsion for his doctoral thesis in 1937, Frank Malina mentioned to Fritz Zwicky of Caltech some difficulties he was having in his study. Zwicky exploded with the opinion that Malina was wasting his time on an impossible subject. For, he said, Malina must realize that a rocket could not operate in space as it required the atmosphere to push against to provide thrust! By 1940 he realized that he was mistaken.
At Guggenheim Aeronautical Laboratory, California Institute of Technology (GALCIT),in 1939, one of the first objectives was to develop a solid propellant rocket unit capable of delivering a constant thrust on the order of 1000 pounds for a period of 10 to 30 seconds. As far as is known, no black powder or smokeless powder rocket had ever been constructed to meet these specifications of thrust and duration. Experts consulted by Malina, John Parsons, and Forman were very dubious about the possibility of doing so.
Preliminary experiments made by Parson and Forman with pressed solid propellant charges restricted to burn cigarette-fashion appeared to support this view. It was generally believed that the combustion chamber pressure of a restricted burning solid rocket unit would continue to rise from the moment of ignition until any combustion chamber of reasonable weight would burst. In other words, it was thought that such combustion was inherently unstable.
The GALCIT group's mentor, Professor Theodore von Karman, in the spring of 1940, had to listen to both the opinions of the experts and to the explosions of Parson's rockets. One evening at home Von Karman wrote down four differential equations describing the operation of an ideal restricted burning motor, and asked Malina to solve them. It was found that, theoretically, a restricted burning unit would maintain a constant chamber pressure as long as the ratio of the area of the throat of the exhaust nozzle to the burning area of the propellant charge remained constant, that is, the process was stable. Experimental verification of the theory was soon obtained.
Although there have been centuries of experiments with black powder rocket, and several investigators used smokeless powder and Ballistite in rockets between about 1918 and 1939, none of these rockets had the thrust and duration required for the aircraft "super-performance" applications. Parsons and Forman in 1938 built and tested a smokeless powder constant-volume combustion motor similar to the one that had been used by Goddard. They concluded after these tests that the mechanical complications of constructing an engine using successive impulses to obtain thrust durations of over 10 seconds was impractical. Upon Parson's recommendation, they concentrated their efforts on the development of a motor provided with a restricted burning powder charge that would burn at one end only at constant pressure to provide a constant thrust.
Parsons started with the traditional sky rocket. This type of pyrotechnic device was propelled by a black powder charge pressed into a cardboard combustion chamber with a conical hole in its center. The gases escaped through a rounded clay orifice. Its efficiency was very, very low, but it was reliable. The conical hole in the charge was believed to be the secret that kept the charge from burning down the sides of the container or to produce chamber pressures that would burst the container. The longest duration of thrust of this motor did not exceed about 1 second.
During 1939 and 1940, various mixtures based on black powder and mixtures of black powder with smokeless powder were tested in 1 in. and 3 in. diameter chambers. The charge for the 3 in. chamber was made up of 6 in. long pellets compressed at around 6,500 psi., and coated with various substances to form a solid or liquid seal between the charge and the walls of the chamber. The charge of the 1 in. chamber was pressed directly into the chamber in small increments at pressures between 7,700 and 12,000 psi. Most of the tests of these charges ended in an explosion.
Mechanical causes for failures, such as burning of the charge on the surface next to the wall because of leakage, transfer of heat down the walls sufficient to ignite the sides of the charge, and cracking of the charge under combustion pressure, were suspected. However, there were those who were convinced that the combustion process of a restricted burning charge in a rocket motor was basically unstable. Only after von Karman and Malina proved the process was stable in their analysis of the characteristics of the ideal solid propellant rocket motor in the spring of 1940 was a concentrated effort was made to study the mechanical causes of failure.
Hundred of tests were then made with different powder mixtures, using black powder as the basic ingredient, with various loading techniques and various motor designs. The dependence of chamber pressure on the ratio of chamber cross section area to nozzle throat area was determined for each specific powder mixture.
By the spring of 1941 the results were sufficiently encouraging to schedule flight tests of an aircraft equipped with solid propellant rockets specially designed for it. The propellant charge used in the Ercoupe motor was a type of amide black powder designated as GALCIT 27 (amide: organic compound containing carbon, hydrogen, oxygen, and nitrogen. Some examples: HCONH2, CH3CONH2, C6H13CONH2). The 2 lb. charge was pressed into the combustion chamber, which had a blotting paper liner, in 22 increments by a plunger with a conical nose shape at a pressure of 18 tons. The diameter of the charge was 1.75 in. and its length varied between 10 and 11 in. The motor was designed to deliver about 28 lb. thrust for about 12 seconds.
Eighteen rocket motors were delivered every other day for the first tests at March Field, California, about an hour's drive from the project. During the first phase of the flight tests one motor failed explosively in a static test and one while Ercoupe was in level flight. Thereafter, 152 motors were used in succession without explosive failure. The motors were prepared by Parsons, Forman, and Fred Miller.
On August 16, 1941, Boushey made the first take-off of the Ercoupe with six JATOs firing. The first American manned flight of an aircraft propelled by rocket thrust alone was made by Boushey on August 23, 1941. The propeller of the Ercoupe was removed and 12 JATO units installed, of which only 11 functioned. The Ercoupe was pulled by a truck to a speed of about 25 m.p.h. before the JATOs were ignited. The airplane left the ground and reached an altitude of about 20 ft. This flight was not originally scheduled but the group could not resist the opportunity to make the improvised demonstration of the future possibility of rocket propulsion.
Frank Malina noted that it was most fortunate that the flight tests were carried out close to the location of the project, which permitted the rocket motors to be fired within a few days from the time they were charged with propellant. Following the flight tests, it was found that after the motors were exposed to simulated storage and temperature conditions over several days they exploded in most cases. It was evident that either the blotting paper liner or the mechanical characteristics of the propellant were unsatisfactory.
But the Navy Department regarded the successful Ercoupe tests with much interest from the point of view of application of rockets for assisted take-off of aircraft from aircraft carriers. Upon the urging of Lt. C.F. Fischer of the Bureau of Aeronautics, who had witnessed the tests, a contract was placed by the Navy with the Project in early 1942 for the development of a 200 lb. thrust, 8 second unit. The unit was designated by the acronym JATO for Jet Assisted Take-Off (sometime RATO), and this designation is still used.
This Navy contract came in the midst of the explosive failure of the JATO unit developed for the Ercoupe tests. All efforts to improve the amide-black powder propellant and loading techniques of the motor developed for Ercoupe tests failed to meet specified storage conditions ranging from Alaska to Africa. Investigations of motors using Ballistite also proved negative, mainly because of its ambient temperature sensitivity (variation of its rate of burning and thrust with ambient temperature).
Thus, the spring of 1942 was one of desperation for those concerned with development of a reliable solid propellant JATO unit. They knew that theoretically it was possible to construct such an engine, but no one came forward with a promising idea until June, when Parsons, no doubt after communing with his poetic spirits, suggested trying a radical new propellant. It would consist of potassium perchlorate (KClO4- in place of potassium nitrate KNO3: saltpeter), as oxidizer, common asphalt as used on roads as a binder and fuel. These could be cast, after being mixed, into a combustion chamber.
A test of the propellant, designated GALCIT 53, was quickly made and the results were so promising that work on other propellant types was dropped for a long time. Parsons was assisted in the development of the asphalt base propellant by Mills and Fred Miller. After due study of the origin of the ideas for the new propellant, Parsons was recognized as its inventor and a patent was granted in his name.
At first, the Ordnance Department objected strongly to the use of potassium perchlorate as an oxidizer because it had proved unsafe in the past. Parsons realized that their objection was no longer valid, since way had been found to produce the material with a minimum purity of 99%. Impurities in the form of dangerous chlorates (KClO3) had been practically eliminated. Sodium and potassium chlorates were used with dinitrotoluen in explosives (know as cheddites in French), also with perchlorates and various hydrocarbons-Vaseline-,castor oil, and nitro. Potassium chlorate was also used as oxidizer in matches with phosphorus sesquisulfide P4S3 or tetraphosphorus trisulfide as the active fuel.
The ruling of the Ordnance Department was thereafter changed, allowing the use of this kind of solid oxidizer. The Navy contract for 100 JATO units delivering 200 lb. thrust for 8 seconds was successfully completed, with GALCIT 53 as the propellant. Production of service-type units for the Navy began shortly thereafter at the Aerojet Engineering Corporation (organized at the end of 1941 and formally incorporated on March 19, 1942 with the GALCIT members Von Karman, Malina, Haley, Parsons, Forman, and Summerfield).
The project carried out extensive studies on asphalt-base propellants in the following years. A detailed report released in May 1944 on the propellant GALCIT 61-C by Mills give the following composition: 76% potassium perchlorate and 24% fuel. The fuel component was 70% Texaco No. 18 asphalt and 30% Union Oil Company Pure Penn SAE No. 10 lubricating oil. The fuel was liquefied at about 275 deg F, the pulverized potassium perchlorate added to it, and the mixture thoroughly stirred. The mixture was then poured into the combustion chamber, which had been previously lined with a material similar to the fuel component, and allowed to cool and become hard. This propellant, when burned at a chamber pressure of 2,000 psi., had a chamber temperature of 3,000-3,500 deg F, a specific impulse of 186, and an exhaust velocity of about 5,900 ft. per sec. Storage temperature limits were from -9 deg F to 120 deg F. GALCIT 61-C was developed in 1943 and used in service JATO units by the Navy until the end of World War II. The propellant is also used on the Private A and F research rockets.
IMPROVEMENTS
Solid propellants utilizing potassium perchlorate as oxidizer produced dense clouds of white smoke (potassium chloride-KCl, like sodium chloride-NaCl, common salt), which the Navy did not like at all. Some months after GALCIT 53 was developed, Parsons informed the Project weekly research conference that he had eliminated the smoke problem by replacing potassium perchlorate with ammonium perchlorate (NH4ClO4). Navy rocket experts were immediately invited to visit the Project for a demonstration:
"When they arrived we posted ourselves some distance from the test pit, the red flag was run up, and Parsons gave the order for his latest creation to be fired. We beheld a big cloud of with smoke and Parsons with a look of surprise on his face. He sheepishly explained that the smoke must have been caused by the humidity, for the air had been very dry on the days they had made tests before".
Ammonium perchlorate does reduce the amount of smoke produced if the air is dry, but it produces undesirable chloride in the jet. In fact Cl and H in NH4ClO4 may combine to form HCl, hydrogen chloride or hydrochloric acid with water. But that is the base of modern composite propellants.
The project also studied the possible use of other fuels instead of asphalt, such as Napalm (sodium palmitate = NaPalm - first tried as a high temperature, high energy propellant), gelled hydrocarbons, gelled wax mixtures, and butyl rubber. A continuation of studies of the last material later led Charles Bartley, under the JPL-ORDCIT Project in 1945, to the discovery of the advantages of the castable elastomeric (polysulfide rubber) material called Thiokol. This discovery became the basis of solid propellant manufacture by the Thiokol Chemical Corporation. The Air Force Material Command terminated work by the Project on solid propellant motors on June 30, 1944. The Ordnance Department, however, continued the work for long range missile applications.
During the course of this research, engineers were provided with methods of motor component design when the following characteristics of the propellant to be used were known:
- Sensitivity of the propellant to ambient temperature during combustion.
- Combustion pressure limit below which the propellant burns in irregular manner.
- Combustion pressure limit above which the propellant burns in an unpredictable manner.
- Storage characteristics of the propellant charge from the point of view of minimum and maximum ambient temperatures allowed and possible decomposition of the propellant with prolonged storage.
- Ignition temperature of the propellant.
- Rate of burning of the propellant as function of the combustion pressure.
- Performance characteristics of the propellant to produce rocket thrust.
The great progress made in the scientific design of solid propellant rocket motors in comparison with the empirical, traditional, method used in previous centuries can be appreciated by reference to the text "Jet Propulsion" prepared for the course at Caltech at the request of the Air Technical Service Command in 1943 and continued in the following years. The debate on the superiority of solid vs. liquid propellant rocket engines for boosters of space vehicles still rages today (but environmental considerations now favor liquid propellants).
Sponsorship of solid-propellant research was taken over by the ORDCIT Project from the Air Force Materiel Command on July 1, 1944. By this time, JPL had made the following fundamental contributions to the design and construction of long-duration solid-propellant engines:
- Theory: Von Karman-Malina theory of constant-thrust long- duration engines (1940)
- Propellant development:
- Parsons' break-away from Ballistite with amide black powder (1940)
- Parsons' introduction of perchlorates as an oxidizer (1942).
- Parsons' introduction of asphalt as fuel-binder with perchlorates; the invention of a castable case- bonded composite propellant charge (1942).
- Engine component design
- Parsons' design of a restricted-burning (case- bounded) propellant charge with amine black powder (1940).
- Malina-Mills design of a safety pressure relief valve (1942).
- Mills' review of various types of burning surfaces of a charge and theoretical confirmation that the surface of a cigarette-type burning charge was stable (1943).
After the successful JATO development with the asphalt- perchlorate propellant in 1942, Mills sought a fuel-binder for the perchlorate superior to asphalt. In 1944, Charles Bartley joined Mills' group, and in 1945 introduced as a replacement for asphalt a castable elastomeric material, polysulfide rubber, produced by Thiokol Chemical Corporation. The polysulfide rubber, compared to asphalt, produced a propellant much better both as regards storage temperature limits and hardness at high atmospheric temperatures. The latter property was especially important in the design of high-thrust engines requiring a charge with an internal-burning surface rather than a cigarette-burning surface.
Since at this time only Aerojet in the USA was producing composite solid-propellant engines, that company's attention was drawn to the asphalt replacement, but it was already interested in a similar material made by the General Tire and Rubber Co. It was only at the urging of the Ordnance Department that the Thiokol Chemical Corp. entered the field of composite solid propellants with the new fuel-binder discovered at JPL.
After obtaining the experience with the composite solid- propellant missiles Private A and F, studies began at JPL in 1946 on larger missiles using, in particular, the polysulfide rubber-perchlorate type propellant. The results of these studies led eventually to the design of the tactical guided missile, Sergeant.
The laboratory followed closely development with other type of solid propellants, especially Ballistite, used in high-thrust short-duration engines suitable for boosters (Aerojet built some double-base boosters using this material).
Other special-purpose rocket vehicles supported research in solid propellants and high-acceleration, and high-speed dynamics. A small vehicle unofficially called "Thunderbird" demonstrated the polysulfide composite-propellant, internal-burning star-grain solid motor in 1947. With an acceleration of over 100 G, (a precursor of the Sprint missile) it led to the Wac-scale solid-propellant research vehicle called Sergeant in 1948.
This Sergeant sounding rocket, unrelated to the tactical missile of the same name, proved to be ahead of its time. It was inspired by calculations that indicated a solid-propellant rocket of the internal-burning-star design could deliver several times the payload of a liquid-propelled V-2 type of similar weight. The motor chamber walls were very thin because the propellant, burning from within, would help contain heat and pressure.
An autopilot design effort was begun, and static tests of the motor, weighing 1300 lbs and delivering about 6000 lbs thrust for more than 30 seconds, were conducted.
Difficulties with this solid rocket, manifested in the rupture of the thin-wall case, coincided with a change in the JPL mission and an acceleration and expansion of Corporal development. The Sergeant project was suspended. The electronic autopilot was adopted for the Corporal missile while the solid-propellant engineers took their problems back to the laboratory and test stand for more investigation. Further development was undertaken by the Thiokol Chemical Corporation. The ultimate heritage of this early "Sergeant" powerplant was the reliable solid rocket, used in large scale in the Sergeant and other military missiles, and in clustered miniatures to launch the first Explorer satellites.
The motor evolved from the Sergeant test vehicle of 1948-49 via the Hermes RV-A-10 flight tested in March 1953. A Hermes A-2 Thiokol motor was ground tested in December 1951. The Hermes A-2 program was ended in October 1952.
The Sergeant missile was not the only result of the Thiokol polysulfide motor. Another major development was the Nike-Hercules sustainer motor (or stage two), the Lacrosse motor, and later the Bomarc B motor. Many small missiles, sounding rocket motors, and the Mercury and Gemini retro-rockets used the same propellant.
However, the use of polysulfide by Thiokol probably caused their loss of the key Polaris contract. Aerojet won the contract with the use of a more energetic polyurethane propellant.
After that Thiokol began the use of polybutadiene for big motors and won the contract for the Minuteman first stage motor. That lead as well to the Nike-Zeus, Pershing, Castor motors, Surveyor retro (first of a series of upper stage motors) and finally to the Shuttle SRB's.
Meanwhile, Hercules began the use of double-base propellant as fuel in composite propellants, since double-based motors burned with excess of fuel. The use of a separate oxidizer also permitted the addition of energetic fuels such as aluminum powder.
The excess of fuel in pure double-base caused a long afterburning flame, essentially of burning carbon (see launch-photographs of Nike Ajax and Hercules, Honest John, Terrier, and Talos). The unburned carbon cause also the dark exhaust before the afterburning.
The Hercules' Minuteman third stage was a follow-on of the Vanguard third stage.
Some composite propellants continue to use saltpeter (potassium nitrate) or ammonium nitrate.
Some composite propellant formulations and characteristics:
- Molded composite: potassium nitrate(20-50%), elastomer(10%), ammonium picrate-NH4C6H2NO7-(70-40%). Specific impulse s.l.: 160 to 200 sec. Abundant smoke. Hard to brittle.
- Castable composite: ammonium nitrate(80%), elastomer (18%), catalyst(2%). Specific impulse s.l.: 185 to 198 sec. Little smoke. Soft and resilient to hard and tough.
- Castable composite: ammonium perchlorate(50-85%), elastomer(50-15%). Specific impulse s.l.: 175 to 240 sec. Much smoke at low oxidizer; little at high oxidizer; mist at relative humidity greater than 80%. Soft and resilient to hard and tough.
- Castable composite: potassium perchlorate(50-80%), elastomer(50-20%). Specific impulse s.l.: 165 to 210 sec. Abundant smoke. Soft and resilient to hard and tough.
OXIDIZERS
Ammonium perchlorate is the most widely used today. It is characterized by high heat, is a good gas producer (not a smoke producer), percent of oxygen by weigh: 34 percent, specific gravity: 1.9.
Potassium perchlorate is used for fast burning rates. It is characterized by high heat, is a low gas producer, percent of oxygen by weight: 46 percent, specific gravity: 2.5.
Ammonium nitrate is used for slower burning rates. It is characterized by low heat, is a high gas producer, and is good for gas generator propellants. It requires a greater amount of binder (fuel) to make castable, but too much binder produces excessive smoke. Ammonium nitrate's percent of oxygen by weight: 20 percent, specific gravity: 1.9. It may be the oxidizer for the future. It contains no toxic elements and no solid elements, produces no solids by decomposition, and therefore, together with a high energy non-polluting fuel, could provide a more 'environmentally friendly' solid propellant.
Lithium perchlorate, a proposed oxidizer, is very hygroscopic and may be used in some high-temperature propellants. Percent of oxygen by weight: 60 percent, specific gravity:2.4.
BINDER SYSTEMS
Introduction
The original composite propellants, used in JATO units, contained an asphalt binder. Since asphalt-perchlorate composites had poor performance and formulation characteristics, extensive research and development work was directed toward their improvement. This soon led to the discovery and acceptance of new and better chemical binder-fuels, primarily synthetic rubbers Initially, polysulfide liquid polymers were developed with only physical properties that were an improvement over those of asphalt. Later, with certain chemical-structure modifications, the overall performance of polysulfide soon outshone that of asphalt. Polysulphides, however, had a major drawback in that they released water during combustion; which interfered with efficient burning. The water by-product also limited the type of additives that could be mixed with the propellant, since water was highly reactive with materials such as aluminum. In the search for binder-fuels without the drawbacks of asphalt and polysulfides, polyurethanes (synthetic thermosetting or thermoplastic polymers) were found to have good performance and physical properties. With these aluminum could be incorporated for higher specific impulse. However, polyurethanes were so viscous that the amount of oxidizers and other solid additives that could be incorporated was limited. Eventually polybutadiene- based propellants were developed that had physical properties superior to those of polyurethanes.
Polysulfide
Polysulfide was the first binder elastomer fuel. For rocket applications a low-molecular-weight polymer was made from dichlorodiethyl formal; sodium polysulfide was used as the liquid binder. When the mixture was heated with an appropriate curing agent such as zinc oxide, the links between adjacent polymer chains were joined together to form the rubber network. The resulting binder had a glass-transition temperature near -60 deg F., making it usable to about -40 deg F. This was a distinct advantage over the first composites.
An undesirable quality of the polysulfides was the presence of sulfur atoms in the system. They produced high-molecular-weight exhaust products (sulfur dioxide with a molecular weight of 64) thereby lowering specific impulse. Since a large amount of oxidizer had to be mixed with the binder to obtain the high energy desired, the binder lost much of its rubber-like quality.
There were many organic and inorganic materials that acted as oxidizers and could be used to cure liquid polysulfide polymers. Each had its advantages and disadvantages.
Thiokol developed many varieties of polysulfides with improved qualities.
Polyurethane
Polyurethanes were the second elastomer fuel binder. The group of polymers known as polyurethanes were made by combining polyols with isocianates. The versatility in polymer chemistry was such that a large number of starting materials having varying molecular weights were available.
Compared with the polysulfides, the average molecular weight of the polyurethanes' exhaust gases was lower. This was because the polyurethanes contained only carbon, hydrogen, oxygen, and nitrogen atoms (not sulfur). An additional benefit was claimed in the processing: the backbone polymer contained substantial amounts of oxygen. It was not necessary therefore to use as great a percentage of oxidizer in the formulation of the propellant to achieve comparable energies. The increased proportion of binder to oxidizer provides added elongation and other good mechanical properties to the propellant, permitting the addition of other energetic fuels (for example aluminum).
From the logistics standpoint, the starting ingredients for manufacturing polyurethane were available from a large number of chemical suppliers, whereas the liquid polysulfide rubbers were manufactured almost exclusively by a single company. This had its effect on cost, quality, and delivery time.
One of the advantages of polyurethane was that a high concentration of nitrate ester could be incorporated in the binder to give increased energy. A commonly used polyurethane binder material was ESTANE, a product of B.F. Goodrich Chemical Company.
Polybutadiene.
Polybutadiene Acrylic Acid.
Almost concurrently with the evolution of the polyurethane propellants, a new type of binder based on long-chained polybutadiene backbone gained the attention of rocket manufacturers. The selection of polybutadiene binder for propellants to be used over wide temperature ranges was a natural one, since most butabiene copolymers (butadiene-styrene, butadiene-acrylonitrile, butadiene- methylvinyl pyridine) had glass-transition temperatures near or below -100 deg F. This was advantageous, since the mechanical behavior of a propellant during periods of strain was related to its properties at different temperatures. For example, the ability of a propellant to withstand high strain rates such as those encountered on ignition of a large-diameter rocket motor was directly related to low-temperature properties such as elongation and brittle point. Therefore, the polybutadiene propellants were attractive, both for large motors and for those requiring wide temperature ranges of operation.
Probably the most widely used polybutadiene polymer (1967) had been PBAA, a copolymer of polybutadiene and acrylic acid. One of the added benefits of PBAA over polyurethane was that the binder system was less complex, consisting essentially of the liquid polymer and a single curative chemical such as an epoxide resin. In certain formulations where a large amount of oxidizer and an auxiliary metal-powder fuel such as aluminum was needed to provide high energy, it was necessary to add to the binder a liquid hydrocarbon or other low-viscosity fluid that acted as a plasticizer to aid in processing.
By contrast, the polyurethane system normally consisted of a main chain polymer such as a polyether diol, a shorter chain cross-linking agent (perhaps a trifunctional polyol), a curing agent (isocyanate) and a curing catalyst; polyurethanes also employ plasticizers where necessary, usually in the form of aliphatic esters such as dioctyladipate or dioctylsebacate.
Carboxy-Terminated Polybutadiene.
Throughout the 1950's propellant manufacturers depended mainly upon rubber chemicals that were readily available to provide the material used in the binders. Among these were PBAA, and the polyethers and polyesters used in polyurethane propellants.
However, at the beginning of the 1960's the designers of weapon systems appeared to be moving ahead of the propellant manufacturers from the standpoint of operational requirements. Thus it was necessary for the propellant research chemist to visualize the "perfect molecular structure" that would best fulfill the need, and then either make the material or work with a chemical supplier to make it.
The first of these custom-made polymers, pioneered by Phillips Petroleum Co. and first evaluated in propellant applications by Rocketdyne, was carboxy-terminated polybutadiene (CTPB). There was an advantage in placing the carboxyl groups at the end of the polymer chain rather than randomly spacing them along the chain (as PBAA polymers). This way the polymer chemist was provided with a uniform structure so he could control his binder network to give the desired mechanical properties. The reproducibility of a controlled system was naturally greater than that of a random structure.
However, the demand by the customer (primarily the US Government) for greater reliability and overall improved performance suggested that still better binders would be forthcoming. To improve reliability of the CTPB system, for example, a greater insight was needed into the affects of molecular weight and molecular-weight distribution. The influence of molecular structure (isomeric configuration) and minor impurities on mechanical properties was to be determined as part of the continuing research and development.
The interplay of mechanical forces between the binder, the aluminium particles, and the ammonium perchlorate crystals would have to be researched until greater knowledge was attained. Information on such fundamentals as energy of wetting, surface free-energy of the solids, the effect of these properties on cracking or other mechanical failure, kinetics of cross-linking reaction, and the effect of temperature and moisture on cure reversion was needed.
There was no doubt that knowledge in these areas would bring about improved hydrocarbon binders.
PBAN - Polybutadiene Acrylic Acid Acrylonitril Terpolymer (PBAN).
This was the formulation widely used on the 1960-70's big boosters (Titan III & Shuttle).
HTPB - Hydroxyl-Terminated Polybutadiene.
HTPB was the most recent state-of-the-art composite propellant binder, manufactured by ATOChem, Inc. (Boosters: Delta II, Delta III, future Delta IV, Titan IVB and Ariane).
NEW BINDERS TO MEET CLEAN AIR REQUIREMENTS.
Environmental concerns regarding the combustion products of large solid rocket motors used in space launch applications led to a number of 'environmentally friendly' binders being proposed.
GAP: Glycigyl azide polymer, a developmental energetic binder produced by 3M Co. and developed at Valcartier, near Québec, Canada.
Poly-NMMO: Poly-nitratomethyl, methyl oxetane, a developmental energetic binder with a high oxygen content, by Aerojet Solid Propulsion Co.
BTTN: Butanetrioltrinitrate, a highly oxygenated energetic plasticiser.
DMBT: Dimethylbitetrazole, a developmental high nitrogen solid fuel with a high positive heat of formation, used in propellants with oxidisers having high oxygen balances to increase performance, developed at NAWCWPNS.
Developments Outside of the USA
Other countries begin to study modern composite propellants around mid-1950. Polysulfide remained a nearly an exclusive product of Thiokol. In 1957 design bureau TsKB-7 in the USSR began the study of solid propellants for the D-6 SLBM system, but the technology was not mature. Beginning in 1961 TsKB-7 build the second and the third stages for the Korolev RT-2 ICBM (US code name SS-13 Savage), but the composite propellant technology in USSR remained many years behind that of the west. The RT-2 first flight was in 1966. Beginning in 1961, development began of the RT-15/8K96 mobile IRBM using two stages from the RT-2. The RT-15 would have a range of 4,500 km with a 1.4 tonne payload. However the project was abandoned in 1970 after 19 test launches.
PROPELLANT ADDITIVES
To help provide the high-energy propellants that were required for the more efficient space vehicles and missiles, many propellants used special fuel additives such as powdered metals. Powdered aluminium was used extensively in propellant formulation for the extra energy it contributed and for the help it gave in promoting stable burning. Although powdered beryllium had a higher theoretical energy value than aluminium, it was seldom used because of its extreme toxicity, relative scarcity, and higher cost. In addition, beryllium had a poor combustion efficiency with most of the hydrocarbon binder-fuels available. However, this could be improved by using it with unique and advanced binders like fluorocarbons.
THE SEARCH FOR HIGH ENERGY PROPELLANTS
After WW II, with the Cold War and the prospect of space travel, the search for exotic, energetic fuel was the rule. Boron was the star during the 1950s, but things changed during the 1960s and 1970s. Rocket fuel selection began with an evaluation of the elements from which candidate fuels were, or may be composed. The calculated variation in adiabatic combustion temperature for an oxygen reaction with some of the elements had been reported by Grosse and is reproduced in the table here.
These temperatures varied considerably and showed that some heavy elements were capable of producing even greater temperatures than light elements such as hydrogen and carbon. However, the heavy elements could quickly be eliminated from consideration (however note that the combustion temperatures would be different with fluorine or other oxidisers). A few, such as zirconium and titanium, were merely competitive on a volumetric heating value basis (BTU/cu ft) and considerably inferior on a gravimetric basis (BTU/lb). Light elements, such as hydrogen, lithium, beryllium, boron, carbon, magnesium and aluminium, appeared interesting.
Only hydrogen, beryllium and boron had higher heating value than the usual hydrocarbons (HC=~18-19). Beryllium was scarce and extremely toxic, and does not at this time merit serious consideration. High energy fuels, therefore, quickly become restricted to hydrogen and boron and a few classes of compounds containing hydrogen or boron. Special purpose fuels could also involve compounds containing lithium, magnesium, aluminium or carbon. (if one notes that a lighter element goes faster (exhaust velocity) for the same combustion temperature, it can be seen that the carbon and sulphur of black powder, and the sodium in Napalm, were very poor fuels).
EXTOTIC, HIGH ENERGY SOLID PROPELLANTS - THE VIEW IN THE 1960s.
Space and military applications stimulated chemical research so that many exotic and highly reactive ingredients for solid-propellant rockets were produced.
The oxidisers in use consisted of weakly held oxygen atoms in chlorine and nitrogen compounds. It was thought that future oxidisers would have less chlorine and nitrogen atoms, and most of the oxygen would be replaced by fluorine. Some oxygen would remain for the purpose of burning the carbon in the binder to carbon monoxide. Fluorine would be linked to oxygen and nitrogen atoms, with which it forms weak bounds. Nitronium perchlorate and its fluorine derivative (nitronium perfluorate?) were outstanding oxidisers at that time.
Fuels would be light-metal hydrides then known, but efforts would be made to replace these by less reactive hydrides of mixed nature. The fuel would be a light-metal hydride with a low heat of formation-one which yields fluorides and oxides with the highest heat of formation. Since rockets using exotic propellants would have a limited volume, the density of the propellant was of critical importance. The best fuels would be light-metal hydrides of low density, a factor which must be considered in the selection of the oxidiser and binder.
A major problem was to solve that of preventing the oxidiser and fuel from reacting with each other and with the organic polymeric binder material. Binders would have to be developed which were inert to the fuel and oxidiser. In addition, binders would have to prevent chemical interaction of fuel and oxidiser to avoid possible propellant explosions. The most likely binders would contain long chains of carbon atoms bearing fluorine atoms- (CF2)n -fluorocarbons). The fluorine would serve to consume the fuel and produce inert polymers. These binders would contain little hydrogen since the metal hydrides contained loosely held hydrogen. The performance of these future solid propellants would probably range from 285 to more than 300 seconds. The ultimate solid propellant (specific impulse of up to 350 seconds) would be composed of a binder containing sufficient oxygen to convert its carbon monoxide. A maximum of fluorine-oxygen-carbon groups was also desirable.
Binders more dense than the (CF2)n structure previously mentioned would be difficult to achieve since its density was 50 to 60 percent greater than conventional hydrocarbon binders. In view of compatibility problem with solid propellants, hybrid-propellant systems would have to be developed. Some liquid fuels and oxidisers were superior to their solid counterparts, so the hybrid system should be able to achieve performances which were superior to those of solid propellants.
EXOTIC INGREDIENTS - THE VIEW IN THE 1960s
The development of propellants with higher energy (250-300 Isp) and increased thermal stability (300°F- 500°F) necessitated the incorporation of some exotic chemicals into solid propellants and related devices. Many of these compounds had unusual hazards associated with their uses that were not immediately evident. Others had been used in various phases of research and development and had recognised toxic or explosive properties. The following section lists, with brief comments, some of the more important of these chemicals that were then used in the development of new propellants.
OXIDIZERS.
- Nitronium perchlorate or NP (NO2ClO4)-Nitrosyle
- Toxicity- Decomposes above 80°C or in contact with water and many organic compounds. The decomposition of NP releases oxides of nitrogen (NO,NO2) and chlorine (Cl2). Maximum allowable concentration are 5 ppm.
- Sensitivity- Mixtures of NP with nearly all organic compounds are dangerous and explosives and are apt to explode spontaneously. Mixtures with other oxidisable materials behave similarly.
- Uses- Proposed for use in high-energy propellants.
- Lithium perchlorate or LP (LiClO4)
-
Toxicity- Not toxic unless large amounts taken orally.
- Sensitivity- Same as potassium perchlorate. Mixtures with reducing agents are explosives (class B).
- Uses- High-temperature propellants.
- Hydrazinium diperchlorate or HP (N2H6(ClO4)2)
-
- Toxicity- Decomposes to give chlorine gas (Cl2).
- Sensitivity- Very hazardous material to handle. Extremely
sensitive to impact and friction. Low auto-ignition
temperature.
- Uses- High-energy propellants.
FUELS
BINDERS
- Nitrourethanes or NU
-
Toxicity- All nitro compounds are toxic, some extremely so. Many are absorbed through the skin. Some may cause dermatitis. The alisocyanates from which nitrourethanes are prepared are extremely hazardous.
- Sensitivity- Nitrourethanes are generally class-C explosives, but a few may be more sensitive.
- Uses- High energy propellants.
- Nitramines (HMX, RDX)
-
Toxicity- Most similar to nitro compounds but more variable, depending on structure. Some may cause severe dermatitis.
- Sensitivity- Some are class-B explosives. Nitrourethanes mixed with this group are generally class C.
- Uses- Experimental only. (1967)
- Tetrazoles
-
Toxicity- Toxic properties not well established but some are apparently non-toxic.
- Sensitivity- Some propellants and pyrotechnic devices using tetrazoles accidentally exploded, causing several injuries. These devices are regarded as extremely hazardous.
- Uses- Various pyrotechnic devices.(derivatives in high-energy propellants)
- Fluorocarbons or FC
-
Toxicity- While many FC compounds are completely non-toxic, some are extremely toxic. Pyrolysis of many fluorocarbons may yield gaseous, odourless compounds of extreme toxicity. Kel-F, teflon, and other FC polymers release fluorolefins on heating which among the most toxic of gases. Combustion
of FC propellants release toxic gases (hydrogen fluoride).
- Sensitivity- FC derivatives are not explosive unless mixed with certain powdered metals, metal hydrides, and metallorganic derivatives. These mixtures are not easily exploded by shock, but are exploded by heating.
- Uses- Experimental only.
- Plasticizers
-
Toxicity- Many are relatively non-toxic but some of the nitrated or fluorinated materials must be regarded as toxic. Nitrocompounds are absorbed through the skin and cause dermatitis. Dinitriles are toxic; they are absorbed through the skin.
- Sensitivity- All insensitive, except some nitro or nitramino plasticiser.
- Uses- Improved propellants.
Propellant Tables
Calculated Variation In Adiabatic Combustion Temperature
For An Oxygen Reaction With Certain Elements
As Reported By Grosse
Atomic Number | Atomic Weight | Element | Temperature of Combustion deg R | Heating Number Value BTU/LB |
1 | ~1 | hydrogen | ~5,400 | ~52 |
2 | ~4 | helium | inert |
3 | ~7 | lithium | ~4,700 | ~18 |
4 | ~9 | beryllium | ~7,900 | ~28 |
5 | ~10 | boron | ~5,400 | ~26 |
6 | ~12 | carbon | ~3,700 | ~14 |
7 | ~14 | nitrogen | ~( 2,200) | quasi-inert with O |
8 | ~16 | oxygen | .......... | oxidizer |
9 | ~19 | fluorine | .......... | oxidizer |
10 | ~20 | neon | .......... | inert |
11 | ~23 | sodium | ~3,800 | ~4 |
12 | ~24 | magnesium | ~6,100 | ~11 |
13 | ~27 | aluminum | ~7,000 | ~13 |
14 | ~28 | silicium | ~4,600 | ~12 |
15 | ~31 | phosphorus | ~(2,400) | ~11 |
16 | ~32 | sulphur | ~(1,800) | ~4 |
17 | ~35 | chlorine | ~(400) | oxidizer |
18 | ~40 | argon | .......... | inert |
19 | ~39 | potassium | ~3,100 | ~2 |
20 | ~40 | calcium | ~6,900 | ~7 |
21 | ~45 | scandium | ~7,100 | ~8 |
22 | ~48 | titanium | ~6,000 | ~9 |
23 | ~51 | vanadium | ~6,000 | ~7 |
24 | ~52 | chromium | ~6,000 | ~6 |
25 | ~55 | manganese | ~6,200 | ~5 |
26 | ~56 | iron | ~5,500 | ~4 |
27 | ~59 | cobalt | ~(4,300) | ~3 |
28 | ~59 | nickel | ~(3,000) | ~2 |
29 | ~64 | copper | ~2,200 | ~1 |
30 | ~65 | zinc | ~4,000 | ~3 |
31 | ~70 | gallium | ~4,900 | ~3 |
32 | ~73 | germanium | ~5,600 | ~3 |
33 | ~75 | arsenic | ~(3,000) | ~3 |
34 | ~79 | selenium | ~(1,700) | ~3 |
35 | ~80 | bromine | ~(400) | oxidizer~2
36 | ~84 | krypton | ~....... | inert |
37 | ~85 | rubidium | ~2,900 | ~1 |
38 | ~88 | strontium | ~6,400 | ~2 |
39 | ~89 | yttrium | ~7,400 | ~3 |
40 | ~91 | zirconium | ~8,700 | ~4 |
41 | ~93 | niobium | ~7,300 | ~3 |
42 | ~96 | molybdenum | ~5,500 | ~2 |
43 | ~99 | technetium | ~........ | ~1 |
44 | ~101 | rubidium | ~........ | ~1 |
45 | ~103 | rhodium | ~........ | ~1 |
46 | ~106 | palladium | ~1,300. | .~1 |
47 | ~108 | silver | ~1,200 | ~1 |
48 | ~112 | cadmium | ~3,100 | ~1 |
49 | ~115 | indium | ~4,100 | ~1 |
50 | ~119 | tin | ~4,900 | ~2,5 |
51 | ~122 | antimony | ~3,100 | ~2 |
52 | ~128 | tellurium | .......... | ~2 |
53 | ~127 | iodine | .......... | ~1 |
54 | ~131 | xenon | .......... | inert |
55 | ~133 | cesium | ~2,700 | ~1 |
56 | ~137 | barium | ~5,400 | |
57 to 71 | | : | | rare earths |
72 | ~178 | hafnium | ~8,700 | |
73 | ~181 | tantalum | ~(7,600) | |
74 | ~184 | tungsten | ~5,800 | |
75 | ~186 | rhenium | ~(4,000) | |
76 | ~190 | osmium | ~(1,800) | |
77 | ~193 | iridium | ~(1,400) | |
78 | ~195 | platinum | ~800 | |
79 | ~197 | gold | ~600 | |
80 | ~201 | mercury | ~1,000 | |
81 | ~204 | thallium | ~(2,000) | |
82 | ~207 | lead | ~3,200 | |
83 | ~209 | bismuth | ~3,600 | |
84 | ~210 | polonium | ~(2,100) | |
85 | ~210 | astatine | ~(1,000) | |
86 | ~222 | radon | ......... | inert |
87 | ~223 | francium | ~2,400 | |
88 | ~226 | radium | ~4,500 | |
89 | ~227 | actinium | ~7,000 | |
90 | ~232 | thorium | ~9,000 | |
Some double-base propellant compositions:
J.P. powder:
Nitrocellulose(13.25%N2): 52.2%
Nitroglycerin: 43.0%
Diethyl phthalate: 3.0%
Diphenylamine: 0.6%
Potassium Nitrate(saltpeter): 1.1%
Nigrosine: 0.1%
J.P.N. powder:
Nitrocellulose(13.25%N2): 51.50%
Nitroglycerin: 43.00%
Diethyl phthalate: 3.00%
Ethyl centralite: 1.00%
Potassium sulfate: 1.25%
Carbon black: 0.20%
Candelilla wax: 0.05%
Slow burning powder:
Nitrocellulose(12.2%N2): 56.5%
Nitroglycerin: 28.5%
Dinitrotoluene: 11.0%
Ethyl centralite: 4.4%
Candelilla wax: 0.1%
---------------------------------------------------
Relative value of Specific Impulse:
Black powder:-----------------------~125 sec.
Double-base:------------------------~200 sec.
Cellulose acetate+ammonium nitrate: ~175 sec.
Asphalt+ammonium perchlorate:-------~180 sec.
Polysulfide+ ":---------------------~200 sec.
Polyurethane+":---------------------~225-230 sec.
Polybutadiene+ ":-------------------~230-235 sec.
Polyurethane+ Aluminum + " :--------~240 sec.
Polybutadiene+ Aluminum + ":--------~245 sec.
PBAA + Aluminum + ":----------------~250 sec.
Composite/double-base:--------------~275 sec.
---------------------------------------------------
List Of Ingredients Used In Double-Base Propellants
Plasticizer (Fuel And Oxidizer)
--NG: nitroglycerin
--TMETN: trimethylolethane trinitrate
--TEGDN: triethylene glycol dinitrate
--DEGDN: diethylene glycol dinitrate
Plasticizer (Fuel)
--DEP: diethylphtalate
--TA: triacetine
--PU: polyurethane
Binder (Fuel And Oxidizer)
--NC: nitrocellulose
Stabilizer
--EC: ethyl centralite
--2NDPA: 2-nitrodiphenilamine
Burning Rate Catalyst
--PbSa: lead salicylate
--PbSt: lead stearate
--Pb2EH: lead 2-ethylhexoate
--CuSa: copper salicylate
--CuSt: copper stearate
--LiF: lithium fluoride
High Energy Additive
--RDX: cyclotrimethylene trinitramine
--HMX: cyclotetramethylene tetranitramine
--NGD: nitroguanidine
Coolant
--OXM: oxamide
Opacifier
--C: carbon black
Flame Supressant
--KNO3: potassium nitrate (saltpeter)
--K2SO4: potassium sulfate
Metal Fuel
--Al: aluminum
Combustion Instability Suppressant
--Al: aluminum
--Zr: zirconium
--ZrC: zirconium carbide
List Of Ingredients Used For Composite Propellants
Oxidizer
--AP: ammonium perchlorate
--AN: ammonium nitrate
--NP: nitronium perchlorate
--KP: potassium perchlorate
--RDX: cyclotrimethylene trinitramine
--HMX: cyclotetramethylene tetranitramine
Binder
--PS: polysulfide
--PVC: polyvinyl chloride
--PU: polyurethane
--CTPB: carboxyl terminated polybutadiene
--HTPB: hydroxyl terminated polybutadiene
Curing And/Or Crosslinking Agents
--PQD: paraquinone dioxime
--TDI: toluene-2,4-diisocyanate
--MAPO: tris(1-(2-methyl) aziridinyl) phosphine oxide
--ERLA-O51O: N,N,O-tri (1,2-epoxy propyl)-4-aminophenol
--IPDI: isophorone diiosocyanate
Bonding Agent
--MAPO: tris( 1-(2-methyl) aziridinyl) phosphine oxide
--TEA: triethanolamine
--MT-4: adduct of 2.0 moles MAPO, 0.7 mole azipic acid,
………and 0.3 mole tararic acid
Plasticizer
--DOA: dioctyl adipate
--IDP: isodecyl pelargonete
--DOP: dioctyl phthalate
Burning Rate Catalyst
--Fe2O3: ferric oxide
--FeO(OH): hydrated ferric oxide
--nBF: n-butyl ferrocene
--DnBF: di-n-butyl ferrocene
--LiF: lithium fluoride
Metal Fuel
--Al: aluminum
--Mg: magnesium
--Be: beryllium
--B: boron
Combustion Instability Suppressant
--Al: aluminum
--Zr: zirconium
--ZrC: zirconium carbide
THERMOPLASTIC BINDERS
Binder Oxidiser Agency Process
Plasticised 50/50 KNO2/Ammonium Monsanto Compression Picrate Formed
Ethyl Cellulose
Polyisobutylene British Compression Formed
Polyvinyl Acetate Ammonium Nitrate Still Limited Use
Polyvinyl Chloride Mix, cast, high temp
THERMOSET BINDERS
Polyester Ammonium Perchlorate Aerojet Cast, cure, cartridge load
Potassium Perchlorate (Aeroplex)
Polysulfide Ammonium Perchlorate JPL/Thiokol Cast in case /case bonded
Butadiene Ammonium Nitrate Phillips Petroleum Extruded-cartridge
Subtopics
| 1.8KS7800 Multiple-source American solid rocket engine. Sparoair II first stage. |
| 100 inch solid Solid propellant rocket stage. Three-segment solid motor proposed for the Solid Titan II in the SLV-4 competition in 1961. Aerojet test fired motors with up to five segments, producing an average thrust of 268,000 kgf for 120 seconds. |
| 15D151 NII-125 solid rocket engine. Designed for first stage of combined missile and SLBM; flight tested, no production. First flight 1967. Solid propellant rocket stage. Four nozzles. Length with interstage 9.8 m. Sea level thrust 60,000 kgf. Specific impulse estimated. |
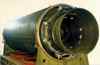 | 15D206 Yuzhnoye solid rocket engine. RT-23 early models stage I. Out of Production. The case-bound T9-BK composite solid propellant charge had a star shape channel. The case was of organic fiber-wound plastic material. |
| 15D23 KBMash solid rocket engine. RT-2 Stage 1. Out of Production. Three gimbaled nozzles for steering. Ammonium perchlorate/aluminum propellant. Chamber pressure 40 kgf/cm2. |
| 15D23P TsKB-7 solid rocket engine. RT-2P Stage 1. Out of Production. Three gimbaled nozzles for steering. Ammonium perchlorate/ammonium butyl propellant. Chamber pressure 56 kgf/cm2. |
| 15D24 TsKB-7 solid rocket engine. RT-2 Stage 2. Out of Production. Three gimbaled nozzles for steering. Ammonium perchlorate/aluminum propellant. Chamber pressure 40 kgf/cm2. Average thrust 33 metric tons. |
| 15D24P TsKB-7 solid rocket engine. RT-2P Stage 2. Out of Production. Three gimbaled nozzles for steering. Ammonium perchlorate/ammonium butyl propellant. Chamber pressure 48 kgf/cm2. |
| 15D25 KBMash solid rocket engine. RT-2 Stage 3. Out of Production. Three gimbaled nozzles for steering. Ammonium perchlorate/aluminum propellant. |
| 15D27 Arsenal solid rocket engine. |
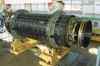 | 15D305 Yuzhnoye, Tsurilnikov solid rocket engine. RT-23 stage I. Out of Production. Case-bound OPAL composite solid propellant charge with a star shape channel. The case was of organic fiber-wound plastic material. R-39 first stage. |
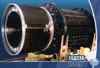 | 15D339 Yuzhnoye. Tsurilnikov solid rocket engine. RT-23 stage II. Out of Production. The case-bound START composite solid propellant charge had a cylindrical-conical umbrella shape channel. The case was of organic fiber-wound plastic material. |
| 15D94 TsKB-7 solid rocket engine. RT-2P Stage 3. Out of Production. Three gimbaled nozzles for steering. Ammonium perchlorate/ammonium butyl propellant. Chamber pressure 48 kgf/cm2. |
| 15Zh58A MITT solid rocket engine. Topol'-M first stage. |
| 15Zh58B MITT solid rocket engine. Topol'-M second stage. |
| 15Zh58V MITT solid rocket engine. Topol'-M third stage. |
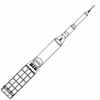 | 160 inch solid Solid propellant rocket stage. Notional 160 inch solid motor considered in cluster of 7 as alternative to Nova 8 F-1 stage. Led to 156 inch motors tested in late 1960's. |
| 2.5KS18000 Multiple-source solid rocket engine. Typical ideal dV=259 m/s; gravity and drag losses = 25 m/s. |
| 200 inch solid segment x 4 Notional solid rocket engine. Study 1960. 4 used as first stage of NASA all-solid Nova design. Extended high-expansion nozzles. Solid propellant rocket stage. Conceptual motor to be used as first stage of a solid Nova design. 4 used as first stage of solid Nova design. Extended high-expansion nozzles. Masses estimated based on total vehicle thrust, performance, and stage volumes. |
| 200 inch solid segment x 6 Notional solid rocket engine. NASA Nova study 1960. 5 used as first stage of solid Nova design. Solid propellant rocket stage. 5 used as first stage of solid Nova design. Masses estimated based on total vehicle thrust, performance, and stage volumes. |
| 22.6KS1245 Multiple-source American solid rocket engine. Sparoair III second stage. |
| 23KS20000 Bristol Aerospace solid rocket engine. Two-finned version. Bristol Aerospace solid rocket engine. Two-finned version. |
 | 240 inch solid Solid propellant rocket stage. Notional 240 inch solid motor considered in cluster of 4 as alternative to Nova 8 F-1 stage. Led to 260 inch motor tested in late 1960's. |
| 26KS20000 Bristol Aerospace solid rocket engine. Four-finned version. Solid propellant rocket stage. Four-finned version. |
| 280 inch solid Notional solid rocket engine. Study 1963. Operational date would have been February 1973 Used on Nova MM 14B launch vehicle. Solid propellant rocket stage. Operational date would have been February 1973. Nova MM 14B first stage. |
| 293-P Kartukov solid rocket engine. P-70 Ametist. Out of Production. |
| 300 inch solid Notional solid rocket engine. Study 1963. Operational date would have been April 1973 Used on Nova MM 14A launch vehicle. Solid propellant rocket stage. Operational date would have been April 1973. Nova MM 14A first stage. |
| 325 in solid Notional solid rocket engine. Study 1963. Recoverable motors; separation at 1,972 m/s at 53,000 m altitude; splashdown using retrorockets under 3 61 m diameter parachutes 610 km downrange. Solid propellant rocket stage. Massed estimated based on tank volumes, total thrust, and first stage burnout conditions. Recoverable stage; separation at 1,972 m/s at 53,000 m altitude; splashdown using retrorockets under 3 61 m diameter parachutes 610 km downrange. |
| 3-DS-47000 Hercules solid rocket engine. X-17 HTV first stage. |
| 5.6KS5400 Multiple-source American solid rocket engine. Nike Viper I second stage. |
| 51T6 Motor Fakel solid rocket engine. A-925 first stage. |
| 53T6 Russian anti-ballistic missile. Endo-atmospheric interceptor component of A-135 ABM system. |
| 5D22 SKB-350 solid rocket engine. A-350Zh second stage. |
| 5S47 SKB-350 solid rocket engine. A-350Zh first stage. |
| 9KS11000 Bristol Aerospace solid rocket engine. |
| 9KS1660 Bristol Aerospace solid rocket engine. |
| A1P-1 Aerojet solid rocket engine. Polaris stage 1. |
| A1P-2 Aerojet solid rocket engine. Polaris stage 2. Polaris AX second stage. |
| A2P-1 Aerojet solid rocket engine. Polaris stage 1. |
| A3P-1 Aerojet solid rocket engine. Polaris stage 1. |
| Acheron French solid rocket engine. Hades first stage. |
| Aerojet SRB Aerojet solid rocket engine. In production. First flight 2002. Solid propellant rocket stage. SRB boosters for Atlas V. Empty mass, vacuum thrust, sea level Isp estimated. |
| Agnes CFTH-HB solid rocket engine. Belisama first stage. |
| Agni engine DRDO solid rocket engine. Agni 2 first stage. |
| Agni St2 DRDO solid rocket engine. Agni 2 second stage. |
| Agni3 S2 DRDO solid rocket engine. Agni 3 second stage. |
| AJ-260-1/3 Aerojet solid rocket engine. Design concept 1960's. Used on Saturn INT-05B launch vehicle. Solid propellant rocket stage. Study NASA 1969. |
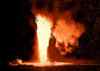 | AJ-260-2 Aerojet solid rocket engine. 260 inch solid rocket booster half length. The version tested and also proposed for use as a first stage with the Saturn IVB. Solid propellant rocket stage. 260 inch solid rocket booster half length. |
| AJ-260X Aerojet solid rocket engine. Study 1967. Full length version of 260 inch motor tested in 1960's. Proposed for use in various Saturn and Nova configurations. Solid propellant rocket stage. 260 inch solid booster - full length. These would have been the flight configuration motors, replacing the Saturn V first stage or being used as booster motors in various Uprated Saturn and Nova configurations. Solid propellant rocket stage. Boeing study, 1969. Solid propellant rocket stage. Boeing Low-Cost Saturn Derivative Study, 1967 (trade study of 260 inch first stages for S-IVB, all delivering 86,000 lb payload to LEO): Low Cost Booster, Solid Propellant. |
| AJ-260X 1/3 Aerojet solid rocket engine. Design concept 1960's. Solid propellant rocket stage. 260 inch solid booster - full length. Saturn 3S second stage. |
| Ajax engine Bell liquid rocket engine for the Nike Ajax sustainer stage. Red fuming nitric acid was the oxidizer; in the test missiles, the fuel was aniline-furfuryl alcohol as fuel, changing to JP-4 kerosene in the production missiles. Nike Ajax second stage. |
| Alcor Aerojet solid rocket engine. Originally developed for the Air Force as a third stage for the Athena sounding rocket; in some applications known as Zebra. One of its main attractions was a very high mass fraction First flight 1960. Solid propellant rocket stage. Masses, specific impulse estimated. |
| Alfa engine Aeritalia solid rocket engine. Alfa first stage. |
| Algol 1 Aerojet solid rocket engine. This rocket started as a Polaris test motor with a 40 inch diameter, which at the time was the largest solid motor ever tested. First flight 1960. Solid propellant rocket stage. This rocket started as a Polaris test motor with a 40 inch diameter, which at the time was the largest solid motor ever tested. It had a nominal performance rating of 45 seconds duration and 45,000 kgf thrust. Variations included Algol I, I-D, II, II-A, II-B and possibly others. Another popular rating was 40KS-115,000 (52,000 kgf for 40 seconds), also known as Senior. |
| Algol 2 CSD solid rocket engine. Used on Scout A, Scout B, Scout X-3, Scout X-4; proposed as strap-on for Titan 3BAS2. First flight 1962. |
| Algol 3 CSD solid rocket engine. Used on Advanced Scout, Scout D, Scout F, Scout G. First flight 1972. |
| Algol 3A CSD solid rocket engine. In Production. |
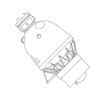 | Alpha Lifeboat Russian manned rescue spacecraft. Study 1995. 1995 joint Energia-Rockwell-Khrunichev design for space station Alpha lifeboat based on the Zarya reentry vehicle with a solid retrofire motor, cold gas thruster package. Five years on-orbit storage. |
| Altair 1 Thiokol solid rocket engine. Used on Atlas Able, Blue Scout 2, Caleb, Delta, Delta A, Delta B, Delta C. First flight 1959. |
| Altair 1A Thiokol solid rocket engine. Used on Scout X-1, Scout X-2, Scout X-3. First flight 1960. |
| Altair 2 Thiokol solid rocket engine. Kick stage motor for Delta D, Scout A, Scout X-4. First flight 1963. |
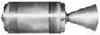 | Altair 3 Thiokol solid rocket engine. In Production. Altair III was developed as the propulsion unit for the fourth stage of the Scout launch vehicle. A filament-wound, fiberglass-epoxy case contained the CTPB propellant grain. |
| Altair 3A Thiokol solid rocket engine. Out of Production. Total impulse 83,839 kgf-sec. Motor propellant mass fraction 0.91. |
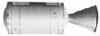 | Altair 3B Thiokol solid rocket engine. In Production. Modified version of the STAR 20 with increased case structural capability over the. A filament-wound, fiberglass-epoxy case contained the CTPB propellant grain. |
| Altair 3D Thiokol solid rocket engine. Kick stage motor for Delta E, Delta L. First flight 1965. |
| Antares 1A Thiokol solid rocket engine. Used on Blue Scout 1, Blue Scout 2, Blue Scout Junior, Scout X-1. First flight 1960. |
| Antares 2 Thiokol solid rocket engine. Used on Scout A, Scout B, Scout D, Scout F, Scout X-2, Scout X-3, Scout X-4. First flight 1962. |
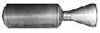 | Antares 3 Thiokol solid rocket engine. In Production. Antares III, third-generation third stage for Scout launch vehicle. Propellant: AP/HTPB/Al propellant in a filament wound Kevlar case. |
| Antares 3A Thiokol solid rocket engine. Out of production. Used on Scout G launch vehicle. First flight 1979. |
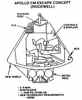 | Apollo CM Escape Concept American manned rescue spacecraft. Study 1976. Escape capsule using Apollo command module studied by Rockwell for NASA for use with the shuttle in the 1970's-80's. Mass per crew: 750 kg. |
| Arcon-1 ARC solid rocket engine. Arcon first stage. |
| Ariane 3-0 P7.35 SNPE solid rocket engine. Strap-on booster for Advanced Scout, Ariane 2/3. First flight 1984. |
| Ariane 4-0 P9.5 SPB SNPE solid rocket engine. Strap-on booster engine for Ariane 42P, Ariane 44LP, Ariane 44P. First flight 1988. |
| Ariane 5-0 P230 SNPE solid rocket engine. In production. Used on Ariane 5 launch vehicle. First flight 1996. Solid propellant rocket stage. Solid rocket booster for Ariane 5. Nozzle expansion ratio increased from 9.7 to 11.0 after 1997. Chamber pressure 61.3 bar. HTPB propellant. |
| Ariane 5-0 P241 SEP solid rocket engine. First flight 2002. Solid propellant rocket stage. Increased propellant loading (+2.43 metric tons), lighter welded case (-1.6 metric tons) compared to earlier versions. |
| Asp II engine Cooper solid rocket engine. Asp III 4L first stage. |
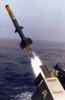 | ASROC Multiple-source solid rocket engine. Terrier ASROC Cajun second stage. |
| Atlas E/SGS-2 American orbital launch vehicle. Atlas E + 1 x Star 48 + 1 x Star 48 upper stages. |
| Aurore SNECMA sounding rocket. Basic single stage vehicle. |
| Bantam Bristol solid rocket engine. Skua first stage. |
| Bantam 2 Bristol solid rocket engine. Skua 2 first stage. |
| Bantam 3 Bristol solid rocket engine. Skua 3 first stage. |
| BB7 Bristol Aerospace solid rocket engine. |
| BE-3 WRE solid rocket engine. SPARTA third stage. |
| BE-3B1 Hercules solid rocket engine. |
| Belier II engine Sud solid rocket engine. Used in single-stage Belier II and as Centaure 2B second stage. |
| Belisama engine CFTH-HB solid rocket engine used in the Belisama and Epona sounding rockets. |
| Black Arrow-3 British solid rocket engine. Out of production. Used on Black Arrow launch vehicle. First flight 1969. |
| BT-310 Japanese single stage sounding rocket. Derivative of S-310. |
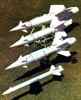 | Bullpup Multi-source solid rocket engine. Bullpup Apache first stage. |
| Burner 2A Solid propellant rocket stage. Burner II was a launch vehicle upper stage developed by Boeing for the Air Force Space Systems Division. It was the first solid-fuel upper stage with full control and guidance capability developed for general space applications. |
| C3-1 Hercules solid rocket engine. Poseidon C3 first stage. |
| C3-2 Hercules solid rocket engine. Poseidon C3 second stage. |
| C4-1 Hercules solid rocket engine. Trident C-4 first stage. |
| C4-2 Hercules solid rocket engine. Trident C-4 second stage. |
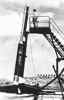 | Cajun The Cajun research rocket was developed as a dimensionally-similar but higher performance successor to the Deacon. Cajun Dart first stage. |
| Canopus IIAE Argentinian solid rocket engine and single stage vehicle. |
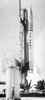 | Castor 1 Thiokol solid rocket engine. Used as apogee kick motor on Delta D, LT Thor Agena D, Scout X-1, Scout X-2, Scout X-3, Scout X-4, TA Thor Agena B, TA Thor Agena D. First flight 1960. M33-20 fourth stage. |
| Castor 120 Thiokol solid rocket engine. Motor similar in size to the Peacekeeper missile stage 1 motor; filled the gap between Castor 4A and the large segmented motors. First flight 1989. Solid propellant rocket stage. Modification of Peacekeeper ICBM first stage. |
| Castor 2 Thiokol solid rocket engine. Used in Scout A; Delta E; H-1-0; Castor 2. License built in Japan for H-1. First flight 1960. Solid propellant rocket stage. Version for Japanese H-1 booster. |
| Castor 4 Thiokol solid rocket engine. Series of motors used as Delta strap-on boosters and as first and upper stages for low-cost all-solid-propellant designs. First flight 1975. |
| Castor 4A engine Thiokol solid rocket engine. Out of production. Castor 4A improved Delta performance by 11% by replacing the old fuel with HTPB propellant. Used in Delta 6900; Atlas IIAS; Castor 4A. First flight 1982. |
| Castor 4AXL Thiokol solid rocket engine. In production. Strap-on booster version, first tested May 1992. Its 30% performance increase would improve performance of Atlas and other vehicles. First flight 2001. Solid propellant rocket stage. Provides supplemental thrust for H-2 or H-2A. Solid propellant rocket stage. Provides supplemental thrust for H-2 or H-2A. |
| Castor 4AXL H-2A Solid propellant rocket stage. Provides supplemental thrust for H-2 or H-2A. |
| Castor 4B engine Thiokol solid rocket engine. Out of production. The Castor 4B, which incorporated thrust vector control in the series for the first time, was developed for ESA's Maxus (first flown in 1991). First flight 1982. Solid propellant rocket stage. Optimized for high altitude (Conestoga). |
| Castor 4BXL Thiokol solid rocket engine. In Production. ORBEX version, combined the 4XL motor with 4B's TVC system (6 degree). |
| Castor 4XL Solid propellant rocket stage. Provides supplemental thrust for H-2 or H-2A. |
| Castor engine Multiple-source solid rocket engine. Out of Production. Used in Jupiter C, Juno 2. First flight 1956. |
| Chick RO solid rocket engine. Skua 3, INTA-255, Petrel zero stage. |
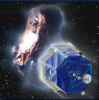 | Contour American Comet Nucleus Tour (CONTOUR) probe. The solid rocket motor that was to boost the spacecraft into solar orbit failed. Multiple comet flybys satellite built by Johns Hopkins University Applied Physics Laboratory (APL) for NASA, USA. Launched 2002. |
| Cuckoo 4 RO solid rocket engine. Skylark 12 third stage. |
| Cuckoo IB RO solid rocket engine. Black Knight 201/C second stage. |
| Cuckoo II RO solid rocket engine. Black Knight 201/C2 second stage. |
| Cygnus 15 Thiokol solid rocket engine. Trailblazer 2 M fourth stage. |
| Cygnus 20 Thiokol solid rocket engine. HJ Nike Nike 20-inch SM fourth stage. |
| Cygnus 5 Thiokol solid rocket engine. Trailblazer 2 M fifth stage. |
| CZ-1D-3 Fourth Academy solid rocket engine. Out of production. Motor for proposed CZ-1D launch vehicle. First flight 1995. |
| D-5-1 Hercules-Thiokol solid rocket engine. Trident D-5 first stage. |
| D-5-2 Hercules-Thiokol solid rocket engine. Trident D-5 second stage. |
| Demon WRE solid rocket engine. HAT first stage. |
| DF-11 Chinese single-stage solid-propellant short range ballistic missile. Export designation M-11, assembled as Ghaznavi in Pakistan. |
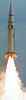 | DF-15 Chinese mobile solid propellant intermediate range ballistic missile. |
| DF-21-1 Shanxi solid rocket engine. First stage of DF-21 IRBM. JL-1 first stage. |
| DF-21-2 Shanxi solid rocket engine. Second stage of DF-21 IRBM. |
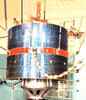 | DFH-2 Chinese military communications satellite. The DFH-2 was a spin-stabilized, drum-shaped military communications satellite with a despun antenna, a diameter of 2.1 m, and a height of 3.1 m. |
| DFH-2 AKM Fourth Academy solid rocket engine. DFH series apogee kick motor. Out of Production. First flight 1984. First use in China of glass fiber wound cases, carbon/carbon nozzle throat insert material, contoured divergent nozzle. |
| DP Boost Solid propellant rocket stage. Boost stage for Tu-123/DP nuclear propulsion upper stage. |
| Dushkin 3M9 Dushkin solid rocket engine. 3M9 Kub. Out of Production. |
| Dynasoar AS American manned spacecraft module. Cancelled 1963. Abort Section, equipped with Thiokol XM-92 Minuteman Stage II motor. Contingency boost. |
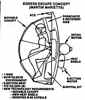 | EGRESS American manned rescue spacecraft. Study 1972. The EGRESS space escape system was based on the proven Encapsulated Ejection Seat System developed for the B-58 bomber in the 1960's. |
| Emilie CFTH-HB solid rocket engine. Grannos first stage. |
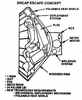 | ENCAP American manned rescue spacecraft. Study 1970. The ENCAP encapsulated bailout-from-orbit concept consisted of a folded heat shield. The astronaut would exit his stranded spacecraft and strap into the seat. |
| EPKM Fourth Academy solid rocket engine. Chinese kick stage for use on CZ-2E for launch of Asiasat-2 and Echostar-1. Diameter increased to 1.7 m in comparison to basic 1.4 m diameter motor. Spin stabilized. First flight 1990. Solid propellant rocket stage. Perigee kick motor for putting CZ-2E payloads into geosynchronous transfer orbit. Thrust, burn time estimated. Specific impulse calculated based on motor payload/delta v performance and masses. |
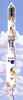 | Excalibur American sea-launched orbital launch vehicle. Excalibur was a subscale version of Sea Dragon proposed by Truax Engineering in the 1990's. It featured the same attributes as Sea Dragon: low cost design (pressure fed engines), LOx/Kerosene first stage (combustion chamber pressure 24 atmospheres) and LOx/LH2 second stage (chamber pressure 5 atmospheres). Guidance would be by a combined Inertial/GPS system. An even smaller Excalibur S vehicle would prove the concept and place 500 kg in orbit. |
| Excalibur Target System The Canadian-made Excalibur Target System was a boosted dart ballistic rocket whose flight could be tailored to simulate various threats for anti-tactical ballistic missile (TBM) system tests. The solid-propellant launched the dart segment to the necessary angle and velocity for the mission. The dart then separated from the booster. It carried a sophisticated electronic RFSAS Radio Frequency Signature Augmentation System, which electronically enlarged the target's radar cross-section to mimic the larger missile appropriate to the mission. |
| Falcon engine Hughes solid rocket engine. Viper Falcon second stage. |
| FFAR American multiple-source air-to-air Folding-Fin Air Rocket, boosted by 1 x Mk7 engine. Unguided fighter weapon, later used as sounding rocket. |
| FFK ERNO solid rocket engine. Forschungsflugkorper first stage. |
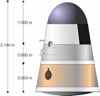 | FSW Chinese military surveillance satellite. Reconnaissance, Earth observation satellite built by CAST, China. Launched 1974 - 1987. |
| FSW Retromotor Fourth Academy solid rocket engine. In Production. Retrorocket designed for deorbit of FSW recoverable satellite. First flight 1975. |
| GCRC GCR solid rocket engine. Used on Vanguard launch vehicle. First flight 1957. |
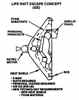 | GE Life Raft American manned rescue spacecraft. Study 1966. The GE Life raft was a rigid unpressurized aeroshell. Three crew in space suits with parachutes would strap themselves into the seats. |
| GEM 40 Hercules solid rocket engine. Air-ignited versions have nozzle ratio of 16:1, specific impulse of 283.4 sec. Used on Delta 7925 launch vehicle. First flight 1990. |
| GEM 46 Hercules solid rocket engine. Air-ignited versions have nozzle ratio of 24.8:1, specific impulse of 284 sec. First flight 1998. Solid propellant rocket stage. Nine 1168-mm (46 in.) diameter Alliant graphite epoxy motors (GEM LDXLs) (strap-on solid rocket motors - SSRMs) augment the first-stage performance of the Delta III and were a direct evolution from the GEMs used on Delta II. |
| GEM 60 Hercules solid rocket engine. In production. Used as strap-on boosters for Delta 3 , Delta IV Medium. First flight 2002. Solid propellant rocket stage. 90.5 bar chamber pressure, 11.0 nozzle expansion ratio. Figures for TVC version. Fixed nozzle version is 599 kg lighter. |
| Gemini AM American manned spacecraft module. 12 launches, 1964.04.08 (Gemini 1) to 1966.11.11 (Gemini 12). |
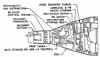 | Gemini B AM American manned spacecraft module. Cancelled 1969. Adapter module for Gemini B, the engines serving as both abort motors during ascent to orbit and for retrofire on return to earth. Abort/deorbit propulsion. |
| GF-02 Fourth Academy solid rocket engine. CZ-1 launch vehicle. Out of production. First upper stage, zero-G, vacuum-start solid rocket motor developed in China. Inserted China's first satellite into orbit on 24 April 1970. |
| GoFast First American civilian sounding rocket to reach outer space. |
| Goldfinch Royal Ordnance solid rocket engine. Out of production. Used on Skylark launch vehicle. |
| Goldfinch II BAJ solid rocket engine. Skylark 6 AC first stage. |
| Goose II RO solid rocket engine. INTA-255 first stage. |
| Gosling 4 RO solid rocket engine. Skylark 10A second stage, INTA-300 first stage. |
| H-1-3 Nissan solid rocket engine. Used on H-1 launch vehicle. First flight 1986. |
| H-2/J-1-1 Nissan solid rocket engine. In Production. Used in J-1-1. |
| H-2-0 Nissan solid rocket engine. Used as strap-on booster on H-2, first stage on J-1. First flight 1994. Solid propellant rocket stage. Shorter monolithic motor using filament-wound case technology from Thiokol. Version for J-1 has 1,000 kg less propellant and 1,200 kg less empty mass than later H-2 SRB. J-1 first stage. |
| HARP-1 Solid propellant rocket stage. |
| HM-16 engine Mitsubishi solid rocket engine. HM-16 first stage. |
| HOTROC NOTS solid rocket engine. Project Pilot first stage. |
| HPAG engine NOTS solid rocket engine. Nike Nike HPAG third stage. |
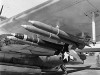 | HVAR American air-to-air rocket. High-Velocity Air Rocket. An unguided fighter weapon, it was later adapted for use by NACA in the early 1950's to boost subscale aerodynamic models to supersonic speed. |
| Hydac Lockheed solid rocket motor. Upper stage for several sounding rockets and test vehicles of 1963-1988. |
| Hyperion-1 Solid rocket stage. 6.00 kN (1,349 lbf) thrust. Mass 100 kg (220 lb). |
| IAI-Arrow-1 IAI solid rocket engine. Arrow 1 first stage. |
| Icarus American sounding rocket, developed by students at Embry-Riddle Aeronautical University in 2003-2007. Took a 7-kg payload to a 61 km altitude. The Loki Research solid rocket engine had a total mass of 44 kg and an empty mass of 4 kg. |
| Icarus St2 Loki Research solid rocket engine. Icarus second stage. |
| Improved Orion engine Aerojet solid rocket engine, originally designed for the Improved Hawk surface-to-air missile. Surplus motors were used in sounding rockets. |
| Iris engine BPD solid rocket engine. Out of production. Used on CZ-1M launch vehicle. CZ-1M third stage. |
| JCR engine Nissan solid rocket engine. JCR first stage. |
| Juno II-3 Aerojet solid rocket stage. 22.00 kN (4,946 lbf) thrust. Mass 100 kg (220 lb). |
| Jupiter C-2 Aerojet solid rocket stage. 80.00 kN (17,985 lbf) thrust. Mass 500 kg (1,102 lb). |
| K10S ISAS solid rocket engine. Kappa 10S third stage. |
| K150 Japanese ISAS sounding rocket. 1/1.6 subscale test rocket used in development of the Kappa 9L sounding rockets. |
| K160 ISAS solid rocket engine. Kappa 8L second stage. |
| K220 ISAS solid rocket engine. Kappa 2 first stage. |
| K245-1 Solid rocket stage. 34.00 kN (7,644 lbf) thrust. Mass 100 kg (220 lb). |
| K250-8 ISAS solid rocket engine. Kappa 8 second stage. |
| K250H ISAS solid rocket engine. Kappa 8L first stage. |
| K420(1/3) ISAS solid rocket engine. Kappa 10S second stage. |
| K420H ISAS solid rocket engine. Kappa 10S first stage. |
| Kappa 5-1 Solid rocket stage. 34.00 kN (7,644 lbf) thrust. Mass 200 kg (441 lb). |
| Kappa 9L-1 Solid rocket stage. 110.00 kN (24,729 lbf) thrust. Mass 1,200 kg (2,646 lb). |
| Kappa 9M-2 Solid rocket stage. 43.00 kN (9,667 lbf) thrust. Mass 300 kg (661 lb). |
| Kartukov LL Kartukov solid rocket engine. LL-1, LL-2, LL-3. Developed 1946-48. |
| Kartukov P-35 Kartukov solid rocket engine. P-35. Out of Production. |
| Kartukov P-5 Kartukov solid rocket engine. P-5. Out of Production. |
| Kartukov P-6 Kartukov solid rocket engine. P-6. Out of Production. |
| Kartukov Soyuz SAS Kartukov solid rocket engine. Soyuz 7K-OK, Soyuz 7KT-OK, Soyuz 7K-T. Out of Production. Thrust 76 metric tons at cutout - 80.1tf at ignition. |
| Kartukov Soyuz T - TM SAS 17k Kartukov solid rocket engine. Soyuz T, Soyuz TM. In Production. Thrust 10 metric tons at cutout - 17.5 at ignition. |
| Kartukov Soyuz T - TM SAS 73k Kartukov solid rocket engine. Soyuz T, Soyuz TM. In Production. Thrust 45 metric tons at cutout - 73 metric tons at ignition. |
| KM-D Nissan solid rocket engine. HIMES Rockoon first stage. |
| KM-H Nissan solid rocket engine. |
| KSR-1 Solid propellant rocket stage. All values except thrust estimated. |
 | KT-1 Chinese all-solid orbital launch vehicle. China's first solid propellant orbital launch vehicle was derived from the first and second stages of the DF-31 ICBM with a new solid third stage. The vehicle was named Kaituozhe-1 (Explorer-1) and was capable of putting 100 kg into polar orbits. |
| L480S ISAS solid rocket engine. Lambda 4T fourth stage. |
| L500 ISAS solid rocket engine. Lambda 4S third stage. |
| L735 ISAS solid rocket engine. Lambda 3 first stage. |
| L735(1/3) ISAS solid rocket engine. Lambda 4SC second stage. |
| Lambda 2-2 Solid rocket stage. 110.00 kN (24,729 lbf) thrust. Mass 1,400 kg (3,086 lb). |
| Lambda 3-2 Solid rocket stage. 110.00 kN (24,729 lbf) thrust. Mass 1,800 kg (3,968 lb). |
| Lambda 3-3 Solid rocket stage. 110.00 kN (24,729 lbf) thrust. Mass 500 kg (1,102 lb). |
| LAPSTAR-300 WRE solid rocket engine. Aeolus first stage. |
| LAPSTAR-52 WRE solid rocket engine. HAD second stage. |
| Lapwing Bristol solid rocket engine. Petrel, Petrel 2 first stage. |
| LK-1 engine IAI solid rocket engine. In production. Lengthened version of Shavit rocket motor. Lower stage used 9:1 nozzle. 23.6:1 nozzle for upper stage use increased Isp to 279 seconds, First flight 1995. Solid propellant rocket stage. Lengthened version of Shavit/RSA-3 rocket motor. For lower stage use with 17.1:1 nozzle. Fitted with 23.6:1 nozzle for upper stage use specific impulse increases to 279 seconds, length to 8.4 m, and empty and gross mass are increased by 135 kg. |
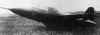 | LL Russian manned rocketplane. Flown 1945. The LL was a transonic aerodynamic test bed authorized by LII in September 1945. Three were built: the LL-1 with a straight wing; LL-2 with a conventional swept wing; and LL-3 with a forward swept wing. |
| Lobster RO solid rocket engine. Jaguar 1 third stage. |
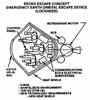 | Lockheed EEOED American manned rescue spacecraft. Study 1966. Lockheed's EEOED was a three-crew Discovery-type re-entry vehicle. |
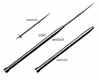 | Loki American GCR unguided solid-propellant barrage anti-aircraft rocket adapted to use as a meteorological sounding rocket. |
| LPC A-1 American solid rocket engine. Apollo LES first stage. |
| LPC-415 Boeing solid rocket engine. |
| LR2-RM-6 Fairchild liquid rocket engine. |
| LS-A Booster Mitsubishi solid rocket engine. LS-A first stage. |
| LS-A engine Mitsubishi solid rocket engine. LS-A second stage. |
| LS-C-2.5 Mitsubishi solid rocket engine. LS-C first stage. |
| LS-C-4 Mitsubishi solid rocket engine. LS-C second stage. |
| Lupus WRE solid rocket engine. |
| Lynx NAWC solid rocket engine. Terrier Lynx second stage. |
| M-10 Nissan solid rocket engine. Mu-4S first stage. |
| M-100-100 Russian solid rocket engine. M-100 second stage. |
| M-100-300 Russian solid rocket engine. M-100B first stage. |
| M-13 Nissan solid rocket engine. Used on Mu-3S launch vehicle. First flight 1969. |
| M14 Nissan solid rocket engine. Used on M-V launch vehicle. First flight 1997. M-V first stage. |
| M-20 Nissan solid rocket engine. |
| M-22 Nissan solid rocket engine. |
| M-23-J Nissan solid rocket engine. In development. Used on J-1 launch vehicle. First flight 1996. Solid propellant rocket stage. Version for J-1 F2 has 300 kg heavier empty mass. J-1 second stage. |
| M-23-Mu Nissan solid rocket engine. Used on Mu-3S launch vehicle. First flight 1969. Mu-3S second stage. |
| M24 Nissan solid rocket engine. Used on M-V launch vehicle. First flight 1997. M-V second stage. |
| M-30 Nissan solid rocket engine. Mu-3D third stage. |
| M34 Nissan solid rocket engine. Used on M-V launch vehicle. First flight 1997. M-V third stage. |
| M-3A Nissan solid rocket engine. |
| M-3B-J Nissan solid rocket engine. In development. Used on J-1 launch vehicle. First flight 1996. |
| M-3B-Mu Nissan solid rocket engine. Used on Mu-3S launch vehicle. First flight 1969. |
| M-40 Nissan solid rocket engine. Mu-4S fourth stage. |
| M55/TX-55/Tu-122 Thiokol solid rocket engine. In production. Proposed as strap-on booster for Saturn IB-C, Saturn INT-14, Saturn INT-15, Saturn INT-19 variants. First flight 2000. Solid propellant rocket stage. First stage of Minuteman I. Proposed as zero stage for various Saturn variants in 1960's. Surplus motors used in ABM SDI tests in 1980's and 1990's. Minuteman first stage. |
| M55A1 Thiokol solid rocket engine. Minuteman 1A T first stage. |
| M56A-1 Aerojet solid rocket engine. Out of Production. Used in Aries. Solid propellant rocket stage. Second stage of Minuteman I. Used as first stage of Aries sounding rocket and various SDI targets in 1980's. |
| M57A1 Hercules solid rocket engine. Hera second stage. |
| M5E1 Hercules solid rocket engine. Nike booster motor. The interstage adapter was bolted to the front of the Nike in sounding rocket applications and lip-fit into the second stage nozzle. Solid propellant rocket stage. The average sea level thrust of the Nike rocket motor was 190.3 kN. The interstage adapter was bolted to the front of the Nike and consisted of a conical shaped adapter which slip-fit into the second stage nozzle, thus providing for drag separation at Nike burnout. Each Nike fin was 0.45 square meters in area. Normally, the fins were canted to provide a two revolutions per second spin rate at Nike burnout. HJ Nike Nike third stage. |
| M-6 Hercules solid rocket engine. Taurus rocket motor originally developed for the Army Honest John tactical missile. In sounding rocket applications the interstage adapter was bolted to the front of the Taurus. Solid propellant rocket stage. Rocket motor originally developed for the Army Honest John tactical missile. In sounding rocket applications the interstage adapter was bolted to the front of the Taurus and consisted of a conical shaped adapter which slip-fit into the second stage nozzle, thus providing for drag separation at Taurus burnout. Each Taurus fin was 0.46 square meters in area. Normally, the fins were canted to provide a two revolutions per second spin rate at Taurus burnout. The weight of the booster system is 3005 pounds. HJ Nike first stage. |
| Mage 1 SEP solid rocket engine. Out of production. Orbital circularization motor. First flight 1979. |
| Mage 2 SEP solid rocket engine. Orbital circularization motor for Advanced Scout, Ariane 2/3. First flight 1984. |
| Mammouth French solid rocket engine. 1900 kg 'Plastolite' propellant. Empty mass estimated. Originally developed as the booster for the SSBT missile. Used on Agate launch vehicle. First flight 1961. |
| MARC 13A1 ARC solid rocket engine. Hydra-Iris first stage. |
| MARC 14A1 ARC solid rocket engine. Boosted Arcas first stage. |
| MARC 14B1 ARC solid rocket engine. Cluster of Sparrow motors. |
| MARC 2B1 ARC solid rocket engine. Boosted Arcas 2 second stage. |
| MARC 2C2 ARC solid rocket engine. Sparrow Arcas second stage. |
| MARC 42A1 ARC solid rocket engine. Boosted Arcas 2 first stage. |
| MARC 60A ARC solid rocket engine. Super Arcas first stage. |
| Martlet 4-1 Bull solid rocket engine. Development ended 1966. Used on Martlet 4 launch vehicle. |
| Martlet 4-2 Bull solid rocket engine. Development ended 1966. Used on Martlet 4 launch vehicle. |
| Martlet 4-3 Bull solid rocket engine. Development ended 1966. Used on Martlet 4 launch vehicle. |
| Mayfly-300 WRE solid rocket engine. Long Tom second stage. |
| Mayfly-600 WRE solid rocket engine. Long Tom first stage. |
| Melanie SEPR solid rocket engine. Out of production. 22 kg propellant. Empty mass estimated. Used on Berenice launch vehicle. First flight 1962. |
| Melusine CFTH-HB solid rocket engine. Grannos second stage. |
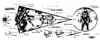 | Mercury American single-crew manned spacecraft. Mercury was America's first man-in-space project, but ran second in the space race, trailing behind the achievements of the Soviet Vostok spacecraft. However lessons learned in Mercury were applied to the follow-on Gemini, which would put America in the space race lead, heading toward final victory with the American moon landing nine years later. ELINT satellite NRO, USA. Launched 1994 - 1998. |
| Mercury Retropack American manned spacecraft module. 18 launches, 1960.01.21 (Mercury LJ-1B) to 1963.05.15 (Mercury MA-9). |
| Meteo-1 Solid propellant rocket stage. |
| Meteor-1 Polish sounding rocket. Single stage vehicle. |
| Meteor-2K The most powerful Polish rocket ever flown. 2 stage vehicle consisting of 2 x Meteor 1 + 1 x Meteor-2. |
| MG-18 LPC solid rocket engine. Scout X-3M fourth stage. |
| MIHT-1 MIHT solid rocket engine. Start-1. In production. Used in Start-1. Estimated values. First flight 1993. Solid propellant rocket stage. All estimated. Start first stage. |
| MIHT-2 solid rocket engine. Start-2. In production. Used in Start-2. Estimated values. First flight 1993. Solid propellant rocket stage. All estimated except stage gross mass. Start second stage. |
| MIHT-3 MIHT solid rocket engine. Start-3. In production. Used in Start-3. Estimated values. First flight 1993. Solid propellant rocket stage. All estimated. |
| MIHT-4 MIHT solid rocket engine. Start-4. In production. Used in Start-4. Estimated values. First flight 1993. Solid propellant rocket stage. All estimated. |
| Mk 104 Thiokol solid rocket engine. SM-3 second stage. |
| Mk 17 Thiokol solid rocket engine. Sidewinder-Arcas first stage. |
| Mk 30 ARC solid rocket engine. SM-1ER second stage. |
| Mk 36 Thiokol solid rocket engine. Sidewinder-Raven first stage. |
| Mk 39 Texas Instruments solid rocket engine for Shrike missile. CleanSweep IIIB first stage. |
| Mk 72 CSD solid rocket engine. SM-2-IV first stage. |
| Mk7 Multiple-source solid rocket engine. Double FFAR second stage. |
| MLRS American tactical ballistic rocket. Multiple Launch Rocket System. US Army assault weapon. |
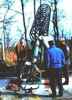 | MMR-06 Russian solid propellant single stage sounding rocket, capable of lofting 5 to 11 kg to 60 km altitude. Launch mass 130 kg, 9 seconds burn time. Nose ejects at apogee. Flown in both conical nose and boosted dart configurations. |
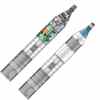 | MOL American manned space station. Cancelled 1969. MOL (Manned Orbiting Laboratory) was the US Air Force's manned space project after Dynasoar was cancelled, until it in turn was cancelled in 1969. The earth orbit station used a helium-oxygen atmosphere. |
 | MOL LM American manned space station module. Cancelled 1969. The Laboratory Module consisted of a forward unpressurized section 2.43 m long, followed by an aft pressurized section, a 3.37 m long cylinder with 2.79 m diameter hemispherical bulkheads at each end. Space station military. |
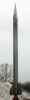 | MR-12 Russian sounding rocket. The MR-12 sounding rocket was developed by the Soviet Union as a modern replacement for the MR-1 Meteo. It was a single stage solid rocket with a 170 kg payload. Payload section 1.55 m long, 0.445 m in diameter. |
| MR-125 LLNL solid rocket engine. Astrid first stage. |
| MR-20 engine Russian solid rocket engine. MR-20 first stage. |
| MR-25 engine Russian solid rocket engine. MR-25 first stage. |
| MSBS 501 Aerospatiale solid rocket engine. MSBS M51 first stage. |
| MSBS 502 Aerospatiale solid rocket engine. MSBS M51 second stage. |
| MSBS 503 Aerospatiale solid rocket engine. MSBS M51 third stage. |
| MT 27 SNECMA solid rocket engine. Lex first stage. |
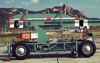 | MT-135 Japanese sounding rocket. The MT-135 was a small single-stage sounding rocket designed to collect data on the middle atmosphere, such as ozone layer depletion. |
| Musca WRE solid rocket engine. Kookaburra second stage. |
| M-V-4 Nissan solid rocket engine. Used on M-V launch vehicle. First flight 1997. |
| NA801 SEREB solid rocket engine. Rubis stage 1. |
| NAL-16 engine Mitsubishi solid rocket engine. NAL-16 first stage. |
| NAL-25 engine Mitsubishi solid rocket engine. NAL-25 first stage. |
| NAL-7 Japanese test vehicle. Single stage vehicle with Mitsubishi solid rocket engine. |
| Neptune engine ONERA solid rocket engine. Second stage of OPd-56-39-22D vehicle. |
| Nihka Bristol Aerospace solid rocket engine. Upper stages. Out of production. The Nihka rocket motor was developed specifically for the Black Brant X rocket system by Bristol Aerospace. Used on Black Brant 10 launch vehicle. First flight 1981. |
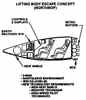 | Northrop LBEC American manned rescue spacecraft. Study 1976. Northrop, building on its work on the HL-10 and M2-F3 lifting bodies, proposed a lifting body three-crew lifeboat. The piloted spacecraft would use a parasail for recovery. |
| NOTS 100A NOTS solid rocket engine. Used on Blue Scout Junior launch vehicle. First flight 1960. Solid propellant rocket stage. Masses, specific impulse estimated. |
| NOTS 124-C NOTS solid rocket engine. X-17 HTV third stage. |
| NOTS 3SM NOTS solid rocket engine. Project Pilot 1 fifth stage. |
| NOTS 8 NOTS solid rocket engine. Project Pilot 1 fourth stage. |
| NOTS-1 NOTS solid rocket engine. Out of production. Used on Caleb launch vehicle. First flight 1960. |
| NOTS-3 NOTS solid rocket engine. Out of production. Used on Caleb launch vehicle. First flight 1960. Caleb third stage. |
| NOTS-4 NOTS solid rocket engine. Out of production. Used on Caleb launch vehicle. First flight 1960. Caleb fourth stage. |
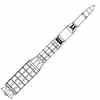 | Nova 5S American heavy-lift orbital launch vehicle. NASA Nova design using segmented solid motors in first and second stages. Five six segment motors in first stage; four four segment motors in second stage, equivalent to 9 x F-1 first stage and 4 x F-1 second stage. |
| NSPO Booster Taiwan-NSPO solid rocket engine. Sounding Rocket first stage. |
| NSPO Sustainer Taiwan-NSPO solid rocket engine. Sounding Rocket second stage. |
| Orbus 1 CSD solid rocket engine. Starbird fourth stage. |
| Oreste ATEF solid rocket engine. Monica I third stage. |
| Oriole Astrotech solid rocket engine. Terrier Oriole second stage. |
| Orion engine Aerojet dual-thrust (boost-sustain) solid rocket engine, originally designed for the Hawk surface-to-air missile. Surplus motors were used in sounding rockets. |
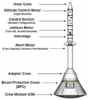 | Orion LAS American manned spacecraft module. Orion launch abort system; consists of launch escape tower, adapter cone, and boost protective cover. Provides emergency crew escape during early boost phase of ascent to orbit. |
| P4 SNPE solid rocket engine. Out of Production. Used on Diamant B launch vehicle. First flight 1970. Diamant BP second stage. |
| P6 SNPE . Out of production. First flight 1965. |
| P80 Fiat-Avio solid rocket engine. In production. Vega's first stage, introduced advanced low-cost technologies that could be reused for future evolutions of Ariane-5 boosters. Solid propellant rocket stage. Vega's first stage, the P80 solid rocket motor, introduced advanced low-cost technologies that could be reused for future evolutions of Ariane-5 boosters. |
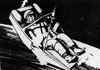 | Paracone American manned rescue spacecraft. Study 1963. The Douglas Paracone was one of the most minimal schemes for bail-out from orbit. The objective was to hit a continental land mass; for such purposes totally manual re-entry operations were used. |
| Peacekeeper 1 Thiokol solid rocket engine. In Production. MX Stage 1. Used as first stage of Taurus launch vehicle for initial test. Solid propellant rocket stage. ICBM MX Peacekeeper ICBM 1st stage. Used for only first Taurus launch. |
| Pegasus XL-1 Hercules solid rocket engine. Used on Pegasus XL launch vehicle. First flight 1994. |
| Pegasus XL-2 Hercules solid rocket engine. Used on Pegasus XL launch vehicle. First flight 1994. |
| Pegasus-1 Hercules solid rocket engine. Used on Pegasus, Taurus. First flight 1989. Solid propellant rocket stage. Pegasus stage 1 without the wings and stabilizers. |
| Pegasus-2 Hercules solid rocket engine. Used on Pegasus, Taurus. First flight 1989. |
| Pegasus-3 Hercules solid rocket engine. Upper stage engine for Pegasus, Pegasus XL, Taurus. First flight 1989. |
| Perigee Orbit Transfer Motor Fourth Academy solid rocket engine. In Production. Basic perigee kick motor for CZ-2E launch vehicle. Featured glass fiber-wound case, HTPB propellant, 3-D finocyl propellant grain, and carbon/carbon throat insert. First flight 1990. |
| Pershing 2 St1 Thiokol, Hercules solid rocket engine. Pershing 2 first stage. |
| Pershing 2 St2 Thiokol, Hercules solid rocket engine. Pershing 2 second stage. |
| Pollux Thiokol solid rocket engine. Little Joe 1 2P first stage. |
| PRD-15 Kartukov solid rocket engine. Strela-1 missile. Out of Production. |
| PRD-19M Kartukov solid rocket engine. KSShch Shchuka. Out of Production. |
| PRD-22 Kartukov solid rocket engine. SM-30. Out of Production. |
| PRD-33 SKB-30 solid rocket engine. |
| PRD-36 Kartukov solid rocket engine. V-600. Out of Production. |
| PRD-52 Kartukov solid rocket engine. DBR-1 Yastreb. Out of Production. Thrust 80 metric tons at ignition, 75 metric tons at cutout. Solid propellant rocket stage. Zero-length launch stage for Tu-121. Thrust varied from 75 to 80 metric tons and duration from 3.75 to 5.0 seconds. |
| PRD-61 Kartukov solid rocket engine. 036 Vikhr. Out of Production. |
| PRD-70 Kartukov solid rocket engine. 400/5V11 stage I. Out of Production. |
| PSLV-1 ISRO solid rocket engine. Used on GSLV, PSLV. First flight 1993. GSLV first stage. |
| PSLV-3 ISRO solid rocket engine. Used on PSLV launch vehicle. First flight 1993. |
| R-31 RV Bus Solid propellant rocket stage. Bus powered by four solid propellant motors mounted 90 degrees to each other, each 60 kg mass, 0.77 m long, 0.28 m diameter. |
| Raven 1 RO solid rocket engine. Skylark 1 first stage. |
| Raven 11 RO solid rocket engine. Skylark 12 second stage. |
| Raven 2 RO solid rocket engine. Skylark 2 first stage. |
| Raven 5 RO solid rocket engine. Skylark 5 first stage. |
| Raven 6 RO solid rocket engine. Skylark 3 second stage. |
| Raven 7 RO solid rocket engine. Skylark 7C second stage. |
| Raven 8 RO solid rocket engine. Skylark 4 second stage. |
| RD RT-1-3 OKB-1 solid rocket engine. RT-1 third stage. |
| RD RT-15-2 OKB-1 solid rocket engine. RT-1 second stage. |
| RD RT-21-2 MITT solid rocket engine. Pioner second stage. |
| RD RT-21-3 MITT solid rocket engine. Temp-2S third stage. |
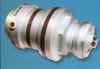 | RD-127 Yuzhnoye solid rocket engine. Maneuvering vehicle bang-bang propulsion, consisted of 25 small solid-propellant motors, probably for homing vehicles or multiple warhead dispensing applications. |
| Redesigned SRM Thiokol solid rocket engine. In Production. Replacement shuttle solid rocket booster with redesigned field joints to prevent failure that caused the Challenger disaster. |
| RH-125 Indian ISRO VSSC sounding rocket. Single stage vehicle |
| RH-125S ISRO VSSC solid rocket engine. Menaka II second stage. |
| RH-200 Indian ISRO sounding rocket. Two stage vehicle consisting of 1 x RH-200 + 1 x RH-125 |
| RH-300-II ISRO solid rocket engine. RH-300 Mk II first stage. |
| RH-560 engine ISRO/Antrix solid rocket engine. RH-560B second stage. |
| RH-75 Indian ISRO sounding rocket. Single stage vehicle |
| Rita II Sud/SEP solid rocket engine. MSBS M2 second stage. |
| RM-1100 Cooper solid rocket engine. |
| RM-1400 Cooper solid rocket engine. |
| RM-3141 GCR solid rocket engine. Jaguar third stage. |
| Rockair American sounding rocket. The Rockair technique (research rocket launched from aircraft) was developed by the Office of Naval Research and the University of Maryland. A 2.75-inch FFAR rocket was fired from a Navy F2H-2 Banshee aircraft to an altitude of approximately 60,000 m. |
| Rook engine Royal Ordnance solid rocket single stage vehicle consisting of a Rook solid rocket motor. Used initially for supersonic tests of aircraft models. The motor was a fast-burning version of Raven. Rook was fired 70 times altogether, in 65 flights and 16 different vehicle designs. |
| RSA-3-1 South African solid rocket engine. Out of production. Built in both Israel and South Africa for RSA-3 and Shavit. Source: Missile exhibit and placards, AF Museum, South Africa. First flight 1988. Solid propellant rocket stage. Source: Missile exhibit and placards, AF Museum, South Africa. |
| RSA-3-2 South African solid rocket engine. In production. Built in both Israel and South Africa for RSA-3 and Shavit. Source: Missile exhibit and placards, AF Museum, South Africa. First flight 1988. Solid propellant rocket stage. Source: Missile exhibit and placards, AF Museum, South Africa. Empty mass includes 583 kg for payload shroud, guidance, orientation and spin-up platform that positions stage 3 and payload for final orbital insertion burn. |
| RSA-3-3 South African solid rocket engine. In production. Israeli AUS-51 rocket motor, built in both Israel and South Africa. Upper stage engine for RSA-3, RSA-4, Shavit, Shavit 1. First flight 1988. Solid propellant rocket stage. Data accurate. Source: Missile exhibit and placards, AF Museum, South Africa. ARC/Rafael AUS 51 is identical. Solid propellant rocket stage. Essentially identical to RSA-3 third stage. Oriented and spun up by 1000 kg avionic section/spin platform, which separates prior to ignition. RSA-4 third stage. |
| RSA-4-1 South African solid rocket engine. Development ended 1994. Used on RSA-4 launch vehicle. Solid propellant rocket stage. Vacuum specific impulse / thrust estimated. Sea level 139,000 kN delivered over 73 seconds. Includes 3400 kg mass of fins, interstage and upper-stage constant-diameter fairing ('sleeve') which is jettisoned after first stage burnout. |
| RSA-4-2 South African solid rocket engine. Development ended 1994. Used on RSA-4 launch vehicle. Solid propellant rocket stage. Essentially identical to RSA-3 second stage. Includes 1000 kg upper stage avionic section / spin table, which is jettisoned prior to stage three ignition. |
| RSRM Thiokol solid rocket engine. After the Challenger disaster the redesigned solid rocket motors had a slight reduction in performance due to reliability improvements. Solid propellant rocket stage. Five-segment version of Shuttle RSRM studied in 1999-2003 to increase shuttle payload to ISS. Test fired in 2003 but not proceeded with. Another version proposed in 2005 for use as lateral boosters for the Constellation Cargo Vehicle. Solid propellant rocket stage. After the Challenger disaster the redesigned solid rocket motors had a slight reduction in performance due to reliability improvements. |
| RT-2-1 OKB-1 solid rocket engine. RT-1 first stage. |
| RTV-100 Aerojet solid rocket engine. |
| RTV-500 Aerojet solid rocket engine. |
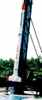 | RX-250-LPN Indonesian sounding rocket. Single stage vehicle. |
| S-160 Japanese ISAS sounding rocket. Single stage vehicle. |
| S-20 Avibras solid rocket engine. |
| S-210 Japanese ISAS sounding rocket. Single stage ionospheric sounding rocket used for research from Japan's Antarctic base. |
| S-23 Avibras solid rocket engine. |
| S-30 engine IAE solid rocket engine. Development ended 1997. VLM fourth stage. |
| S-31 IAE solid rocket engine. |
| S-310 Japanese ISAS sounding rocket. The S-310 was a mid-sized single-stage sounding rocket designed to reach an altitude of 200 km. |
| S-40TM IAE solid rocket engine. Used on VLS launch vehicle. First flight 1985. |
| S-43 IAE solid rocket engine. Used on VLS launch vehicle. First flight 1985. |
| S-43TM IAE solid rocket engine. Used on VLS launch vehicle. First flight 1985. |
| S-44 IAE solid rocket engine. Used on VLS launch vehicle. First flight 1985. |
| S-520 Japanese sounding rocket. The S-520 was a larger single-stage rocket which could be equipped with a three-axis attitude control and a recovery system. It had the capability of launching a 100 kg payload above 300 km and provided more than five minutes of micro-gravity flight for experiments. |
| S-A engine Mitsubishi solid rocket engine. S-A first stage. |
| SA-II engine Mitsubishi solid rocket engine. SA-II first stage. |
| S-B engine Mitsubishi solid rocket engine. S-B first stage. |
| SB-310 ISAS solid rocket engine. |
| SB-735 engine Nissan solid rocket engine. Used on Mu-3S launch vehicle. First flight 1969. |
| S-C engine Mitsubishi solid rocket engine. S-C first stage. |
| SEP 401 Aerospatiale solid rocket engine. MSBS M4 first stage. |
| SEP 402 Aerospatiale solid rocket engine. MSBS M4 second stage. |
| SEP 403 Aerospatiale solid rocket engine. MSBS M4 third stage. |
| SEP 901 Sud/SEP solid rocket engine. MSBS M112 first stage. |
| SEP 902 Sud/SEP solid rocket engine. SSBS S3 first stage. |
| SEP 903 SEP solid rocket engine. SSBS S01 second stage. |
| SEP 904 Sud/SEP solid rocket engine. MSBS M2 first stage. |
| SEPR 685-4 ONERA solid rocket engine. OPd-56-39-22D third stage. |
| SEPR 734-1 ONERA solid rocket engine. Vega Statoreacteur first stage. |
| SEPR 737 ONERA solid rocket engine. VE10A Aigle first stage. |
| SEPR 739-2 ONERA solid rocket engine. Tibere second stage. |
| SEPR 740 SEPR solid rocket engine. Out of production. Used on Berenice, Titus. First flight 1962. Berenice second stage. |
| SEPR 740-3 ONERA solid rocket engine. Titus second stage. |
| SEPR P163 Matra solid rocket engine. Emma first stage. |
| SEPR-732 Sud solid rocket engine. SE4400 first stage. |
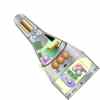 | Shuguang 1 Chinese manned spacecraft. Cancelled 1972. Shuguang-1 (Dawn-1) was China's first manned spacecraft design. The two-man capsule would have been similar to the American Gemini capsule and been launched by the CZ-2 booster. |
| Shuttle ASRM engine Hercules solid rocket engine. Planned replacement for shuttle solid rocket boosters after Challenger disaster. A billion dollars spent in development, but contract terminated. NASA decided to stay with Thiokol RSRM. |
| SICBM-1 Thiokol solid rocket engine. |
| SICBM2 Aerojet solid rocket engine. SICBM second stage. |
| SICBM3 Hercules solid rocket engine. SICBM third stage. |
| SICBM4 Martin solid rocket engine. SICBM fourth stage. |
| Sirocco American sounding rocket. Single stage vehicle using Lockheed solid rocket engine. |
| Skybolt Douglas solid rocket engine. Skybolt ALBM first stage. |
| Skybolt 2 Douglas solid rocket engine. Skybolt ALBM second stage. |
| SLS SRB 2720 Solid propellant rocket stage. Four such 180 inch segmented solid rocket motors provided first stage thrust for Project Lunex. A liquid propellant first stage was considered as an alternative, but the solid stage was the baseline. Empty mass, specific impulse estimated. |
| SLS SRB 388 Solid propellant rocket stage. Booster for SLS A series launch vehicles. |
| SLV-1 ISRO solid rocket engine. Used on ASLV, PSLV, SLV. First flight 1979. |
| SLV-2 ISRO solid rocket engine. Used on ASLV, SLV. First flight 1979. ASLV second stage. |
| SLV-3 engine ISRO solid rocket engine. Used on ASLV, SLV. First flight 1979. ASLV third stage. |
| SLV-4 ISRO solid rocket engine. Used on ASLV, SLV. First flight 1979. ASLV fourth stage. |
| SM3 TSRM Thiokol solid rocket engine. SM-3 third stage. |
| Snipe RO solid rocket engine. Fulmar second stage. |
| SNP Jericho Sud solid rocket engine. Dragon second stage. |
| SO-250 ISAS solid rocket engine. S-250 first stage. |
| Soleil Mammouth French solid rocket engine. 1500 kg Isolane propellant. Used on Topaze launch vehicle. First flight 1962. |
| Soleil NA803 Nord solid rocket engine. 2200 kg Isolane propellant. Stretched version of the NA802. Used on Topaze launch vehicle. First flight 1964. |
| SpaB-54 Fourth Academy solid rocket engine. In Production. Kick stage for orbital insertion of Iridium satellites Used on CZ-2C/SD launch vehicle. First flight 1997. |
| SpaceLoft American commercial suborbital rockets marketed by Up Industries. Data given is for first-launched prototype. |
| SpaceLoft XL American single-stage commercial sounding rocket. Operational, first launch 2006.09.25. |
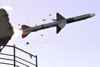 | Sparrow Naval Prop Plant solid rocket engine. |
| SPRAN-50 French solid rocket engine. Daniel first stage. |
| SPRD-15 Kartukov solid rocket engine. S-2 Strela-2 missile, Sopka. Out of Production. Thrust 27 metric tons at cutout - 41at ignition. |
| SPRD-30 Kartukov solid rocket engine. P-15 Termit. Out of Production. Thrust 28 metric tons at cutout - 30 metric tons at ignition. |
| SPRD-99 Kartukov solid rocket engine. MiG-21PFM. Out of Production. |
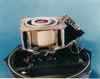 | SPT-100 Stechkin electric rocket engine. Used on Meteor and Gals satellites. In Production. 1.35 kW Hall thruster. Thrust variable 2 to 20 kgf. Marketed in USA by Space Systems/Loral and Fakel. |
| SPT-100-SEP Stechkin solid rocket engine. In Production. The French company SEP is developing this uprated version of the SPT-100 in cooperation with OKB Fakel. |
| SPT-140 Stechkin solid rocket engine. In Production. |
| SPT-200 Stechkin solid rocket engine. In Production. Thrust variable 8 to 80 kgf |
| SPT-290 Stechkin solid rocket engine. In Production. |
| SPT-50 Stechkin solid rocket engine. Meteor-Priroda. In Production. |
| SPT-70 Stechkin solid rocket engine. Yamal. In Production. Thrust variable 1 to 10 kgf |
| SR105 Aerojet solid rocket engine. 12.75" Improved FFAR . |
| SR109 Thiokol solid rocket engine. Maverick AGM-65. |
| SR11 Hercules solid rocket engine. LGM-30 Retro Motor . Used on Minuteman 1 launch vehicle. |
| SR110 Aerodyne solid rocket engine. Super Loki PWN-10, PWN-11, PWN-12. |
| SR113 Thiokol solid rocket engine. HARM AGM-88. |
| SR114 Thiokol solid rocket engine. Maverick AGM-65. |
| SR115 Aerojet solid rocket engine. Maverick AGM-65. |
| SR116 Aerojet solid rocket engine. Sidewinder AIM-9J/P. |
| SR119 Aerojet solid rocket engine. Peacekeeper second stage. |
| SR120 Hercules solid rocket engine. Peacekeeper third stage. |
| SR121 Naval Propellant Plant solid rocket engine. Streaker MQM-107 Booster. |
| SR122 Rocketdyne solid rocket engine. Also designated WPU-9/B1 (AGM-130). |
| SR13 Lockheed solid rocket engine. |
| SR19 Aerojet solid rocket engine. Second stage of Minuteman 2. Surplus motors were used in a variety of anti-ballistic missile test target missiles from the 1980's. |
| SR19/SR19 American target missile. Three stage vehicle consisting of 2 x MLRS + 1 x SR19 + 1 x SR19 |
| SR45 Atlantic Research solid rocket engine. Kitty PWN-6, Rooster PWN-7. |
| SR49 Thiokol solid rocket engine. Genie AIR-2. |
| SR51 Thiokol solid rocket engine. Titan 2 LGM-25C Retro Motor. |
| SR55 United Technology Center solid rocket engine. Titan 2 LGM-25C Staging Motor. |
| SR59 Atlantic Research solid rocket engine. Minuteman 1 LGM-30 Pitch Motor. |
| SR61 Atlantic Research solid rocket engine. Minuteman 1 LGM-30 Spin Motor. |
| SR71 Aerodyne solid rocket engine. Loki PWN-8. |
| SR73 Aerojet solid rocket engine. Minuteman 1 LGM-30 third stage. |
| SR75 Lockheed solid rocket engine. SRAM AGM-69, ASAT ASM-135. |
| SR9 Hercules solid rocket engine. . |
| SRB Thiokol solid rocket engine. Segmented solid rocket boosters for the compromised space shuttle design. Field joint design led to Challenger shuttle disaster. Production 1981-1985, after which superseded by RSRM's. Solid propellant rocket stage. Original configuration. |
| SRB-A Nissan solid rocket engine. In production. Monolithic motor, shorter than that for H-2, using Thiokol filament wound composite structure. First flight 2001. |
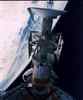 | SRM-1 CSD solid rocket engine. Used in TOS; IUS-1 on Shuttle, Titan 34D. Known by manufacturer as Orbus 21. Propellant: 86% solids made up of HTPB UTP-19360A. Shape: cylindrical. First flight 1982. Solid propellant rocket stage. IUS-2 stage with simplified electronics. |
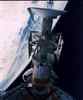 | SRM-2 CSD solid rocket engine. Used in Shuttle, Titan 34D; IUS-2. Known by manufacturer as Orbus 6. First flight 1982. |
| SSUS-A Motor Thiokol solid rocket engine. In Production. A slightly modified stage 3 Minuteman 3 with TVC and roll control systems removed, provided propulsion for the Douglas Spinning Solid Upper Stage for use with Space Shuttle payloads. |
| ST engine Mitsubishi solid rocket engine. ST first stage. |
| ST-735-1 ISAS solid rocket engine. ST-735 1 first stage. |
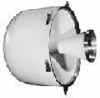 | Star 10 Thiokol solid rocket engine. In Production. SARV Retro MK I was a small, high-performance motor designed for use as a retrograde rocket for an unmanned satellite vehicle. |
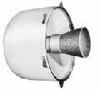 | Star 12 Thiokol solid rocket engine. In Production. SARV Retro, MK IV and V was a 60-pound motor using 40 pounds of propellant. It was designed for use as a retrograde rocket for an unmanned satellite vehicle. |
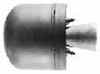 | Star 12A Thiokol solid rocket engine. In Production. Super SARV Retro was a longer, higher impulse version of the STAR 12, used as a retrograde rocket for an unmanned satellite vehicle. |
| Star 13 Thiokol solid rocket engine. Out of Production. A braking motor used by NASA for the Anchored Interplanetary Monitoring Platform program. |
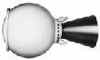 | Star 13A Thiokol solid rocket engine. In Production. Orbit insertion motor incorporated the lightweight titanium case developed for the STAR 13 with the propellant and nozzle design of the earlier TE-M-444 apogee motor. |
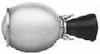 | Star 13B Thiokol solid rocket engine. Out of Production. Orbit insertion motor incorporated the lightweight case developed for the STAR 13 with the propellant and nozzle design of the earlier TE-M-516 apogee motor. |
| Star 13C Thiokol solid rocket engine. Out of Production. Total impulse 8,252 kgf-sec. Motor propellant mass fraction 0.795. |
| Star 13D Thiokol solid rocket engine. Out of Production. Total impulse 7,799 kgf-sec. Motor propellant mass fraction 0.81. |
| Star 13E Thiokol solid rocket engine. Out of Production. Total impulse 6,438 kgf-sec. Motor propellant mass fraction 0.822. |
| Star 13F Thiokol solid rocket engine. Out of Production. Total impulse 9,608 kgf-sec. Motor propellant mass fraction 0.83. |
| Star 15 Thiokol solid rocket engine. Out of Production. Total impulse 11,109 kgf-sec. Motor propellant mass fraction 0.926. |
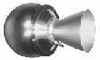 | Star 17 Thiokol solid rocket engine. Skynet 1, NATO 1, and IMP-H & J. Out of production. Used on Atlas LV-3A / Agena D launch vehicle. First flight 1963. |
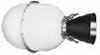 | Star 17A Thiokol solid rocket engine. In Production. Apogee kick motor, modified with 175 mm straight section added to the Star 17. The 17A was used to circularize orbits for the Skynet 1, NATO 1, and IMP-H & J satellites. |
| Star 20 Spherical Thiokol solid rocket engine. Out of Production. Total impulse 30,198 kgf-sec. Motor propellant mass fraction 0.934. |
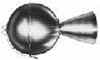 | Star 24 Thiokol solid rocket engine. Skynet 2. In Production. Apogee boost motor was qualified and flown for the Skynet II, later apogee boost motor for NRL and SAMSO. |
| Star 24A Thiokol solid rocket engine. Out of Production. Total flown included in total for Star-24C. Total impulse 50,965 kgf-sec. Motor propellant mass fraction 0.903. |
| Star 24B Thiokol solid rocket engine. Out of Production. Total flown included in total for Star-24C. Total impulse 57,236 kgf-sec. Motor propellant mass fraction 0.915. |
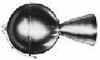 | Star 24C Thiokol solid rocket engine. In Production. Apogee motor designed and qualified for the NASA International Ultraviolet Experiment satellite. |
| Star 25 Thiokol solid rocket engine. Out of Production. Total impulse 61,086 kgf-sec. Motor propellant mass fraction 0.917. |
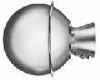 | Star 26 Thiokol solid rocket engine. In Production. Upper stage motor used in the Sandia Strypi IV vehicle. Total flown included in total for Star-26C. Total impulse 62,800 kgf-sec. Motor propellant mass fraction 0.86. First flight 1965. Solid propellant rocket stage. Burner II was a launch vehicle upper stage developed by Boeing for the Air Force Space Systems Division. It was the first solid-fuel upper stage with full control and guidance capability developed for general space applications. |
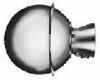 | Star 26B Thiokol solid rocket engine. In Production. Upper stage motor flown on the Burner IIA spacecraft for Boeing and the U.S. Air Force. |
| Star 26C Thiokol solid rocket engine. In Production. Upper stage motor used the titanium alloy case and nozzle attachment ring of the STAR 26B design to provide high propellant mass fraction and was insulated for high-spin-rate applications. |
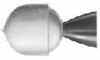 | Star 27 Thiokol solid rocket engine. Apogee motor used on CTS, GMS, BS, GPS, GOES satellites. In Production. |
| Star 27A Thiokol solid rocket engine. In Production. Total flown included in total for Star-27E. Total impulse 89,684 kgf-sec. Motor propellant mass fraction 0.919. |
| Star 27B Thiokol solid rocket engine. In Production. Total flown included in total for Star-27E. Total impulse 92,296 kgf-sec. Motor propellant mass fraction 0.921. |
| Star 27C Thiokol solid rocket engine. In Production. Total flown included in total for Star-27E. Total impulse 88,555 kgf-sec. Motor propellant mass fraction 0.918. |
| Star 27D Thiokol solid rocket engine. In Production. Total flown included in total for Star-27E. Total impulse 88,668 kgf-sec. Motor propellant mass fraction 0.921. |
| Star 27E Thiokol solid rocket engine. In Production. Total impulse 88,301 kgf-sec. Motor propellant mass fraction 0.921. |
| Star 30 Thiokol solid rocket engine. Out of Production. Total flown included in total for Star-30A. Total impulse 136,455 kgf-sec. Motor propellant mass fraction 0.943. |
| Star 30A Thiokol solid rocket engine. Out of Production. Total impulse 137,095 kgf-sec. Motor propellant mass fraction 0.942. |
| Star 30B Thiokol solid rocket engine. Out of Production. Total impulse 148,816 kgf-sec. Motor propellant mass fraction 0.941. |
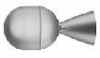 | Star 30BP Thiokol solid rocket engine. In Production. Apogee motor used for the HS 376 satellite bus. Incorporated an 89-percent-solids HTPB propellant in a 6AI-4V titanium case insulated with silica-filled EPDM rubber. |
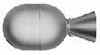 | Star 30C Thiokol solid rocket engine. AS 3000. In Production. Apogee motor used for the RCA G-STAR and Martin Marietta series 3000 telecom satellites. |
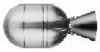 | Star 30E Thiokol solid rocket engine. Koreasat. In Production. Apogee motor used for the BAe Skynet 4 satellite, Koreasat and by the ORBEX small orbital launcher. |
| Star 37 Thiokol solid rocket engine. Total impulse 161,512 kgf-sec. Motor propellant mass fraction 0.899. First flight 1963. Solid propellant rocket stage. Burner II was a launch vehicle upper stage developed by Boeing for the Air Force Space Systems Division. It was the first solid-fuel upper stage with full control and guidance capability developed for general space applications. |
| Star 37B Thiokol solid rocket engine. Out of Production. Total impulse 189,489 kgf-sec. Motor propellant mass fraction 0.91. |
| Star 37C Thiokol solid rocket engine. Out of Production. Total impulse 275,959 kgf-sec. Motor propellant mass fraction 0.921. |
| Star 37D Thiokol solid rocket engine. Out of Production. Total impulse 189,489 kgf-sec. Motor propellant mass fraction 0.91. |
| Star 37E Thiokol solid rocket engine. Out of Production. Total impulse 296,635 kgf-sec. Motor propellant mass fraction 0.926. |
| Star 37F Thiokol solid rocket engine. Out of Production. Total impulse 249,177 kgf-sec. Motor propellant mass fraction 0.928. |
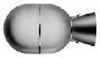 | Star 37FM Thiokol solid rocket engine. In Production. Apogee kick motor for the FLTSTACOM satellite. The motor case contained the same volume as the discontinued STAR 37E. |
| Star 37G Thiokol solid rocket engine. Out of Production. Total impulse 304,620 kgf-sec. Motor propellant mass fraction 0.925. |
| Star 37N Thiokol solid rocket engine. Out of Production. Total impulse 162,102 kgf-sec. Motor propellant mass fraction 0.898. |
| Star 37S Thiokol solid rocket engine. Out of Production. Total impulse 190,590 kgf-sec. Motor propellant mass fraction 0.925. |
| Star 37X Thiokol solid rocket engine. Out of Production. Total impulse 310,668 kgf-sec. Motor propellant mass fraction 0.928. |
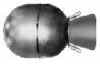 | Star 37XF Thiokol solid rocket engine. Out of Production. Total flown included in total for Star-37XF-8. Total impulse 259,123 kgf-sec. Motor propellant mass fraction 0.929. |
| Star 37XF 8 Thiokol solid rocket engine. Out of Production. Total impulse 238,809 kgf-sec. Motor propellant mass fraction 0.924. |
| Star 37XFP Thiokol solid rocket engine. In Production. Orbit insertion motor qualified for Global Positioning Satellite. Used as a replacement for the discontinued STAR 37F. Propellant: 884 kg of AP/HTPB/Al in 6Al-4V titanium case. |
| Star 37Y Thiokol solid rocket engine. Out of Production. Total impulse 317,856 kgf-sec. Motor propellant mass fraction 0.93. |
| Star 40 Thiokol solid rocket engine. Out of Production. Total impulse 200,882 kgf-sec. Motor propellant mass fraction 0.925. |
| Star 48 Thiokol solid rocket engine. Used in Delta 3900; Conestoga; PAM-S; PAM-D. Total flown included in total for Star-48-8. Total impulse 575,682 kgf-sec. Motor propellant mass fraction 0.946. First flight 1982. |
| Star 48 8 Thiokol solid rocket engine. Out of Production. Total impulse 587,784 kgf-sec. Motor propellant mass fraction 0.945. |
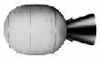 | Star 48A l Thiokol solid rocket engine. In Production. Total impulse 709,062 kgf-sec. Motor propellant mass fraction 0.941. |
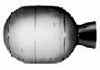 | Star 48A s Thiokol solid rocket engine. In Production. Short nozzle upper-stage motor designed to fit within the dimensional envelope of the long nozzle. |
| Star 48B Thiokol solid rocket engine. In Production. Long nozzle upper-stage motor qualified for the McDonnell Payload Assist Module (PAM) Delta. |
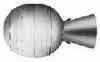 | Star 48B l Thiokol solid rocket engine. In Production. Lengthened version of Star 48B to provide increased payload capability. The design incorporates a longer cylindrical section in the motor case. |
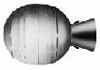 | Star 48B s Thiokol solid rocket engine. In Production. Short nozzle upper-stage motor qualified for the McDonnell Douglas Payload Assist Module (PAM) Space Transportation System (STS). |
| Star 48V Thiokol solid rocket engine. In Production. Developed for Conestoga's upper stage, providing some ±4 degrees capability at 30 degree/sec using the same loaded casing as the 48B. First Flight: 1994. |
| Star 5 Thiokol solid rocket engine. Out of Production. Total impulse 405 kgf-sec. Motor propellant mass fraction 0.87. |
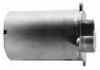 | Star 5A Thiokol solid rocket engine. In Production. Space Gnat was designed to provide a minimum acceleration, extended burn delta-V impulse, for small payload replacement or spin-up applications. |
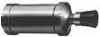 | Star 5C Thiokol solid rocket engine. Out of Production. Titan Retro designed to separate the second stage from the upper stage of the Titan IV launch vehicle. |
| Star 5C/CB Thiokol solid rocket engine. In Production. Titan Retro designed to separate the second stage from the transtage on the Titan II missile and Titan launch vehicle. The motor was also adapted for other uses. |
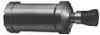 | Star 5CB Thiokol solid rocket engine. In Production. Reduced Al HTPB propellant (2.1 kg) minimizes contamination when Used in a Titan 4 stage separation motor. Diameter: 121 mm. Length: 341 mm. Mass: 4.5 kg. Total impulse: 5.5 kNs. Burn Time: 2.77 sec. |
| Star 6 Thiokol solid rocket engine. Out of Production. Total flown included in total for Star-6A. Total impulse 1,395 kgf-sec. Motor propellant mass fraction 0.795. |
| Star 62 Thiokol solid rocket engine. Out of Production. Total impulse 725,491 kgf-sec. Motor propellant mass fraction 0.94. |
| Star 63 Thiokol solid rocket engine. Used in Shuttle, Titan 34D. Used on Delta 7925 launch vehicle. First flight 1990. |
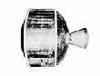 | Star 63D Thiokol solid rocket engine. In Production. Perigee motor with a range of propellant loads, yielding GTO payloads from 3,080 to 4,588 pounds at a constant velocity of 8,012 feet per second. |
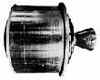 | Star 63F Thiokol solid rocket engine. In Production. Provided perigee kick for the McDonnell PAM-D2 system. Another version was the Star 63D (TU-936). |
| Star 6A Thiokol solid rocket engine. Out of Production. Total impulse 935 kgf-sec. Motor propellant mass fraction 0.723. |
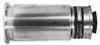 | Star 6B Thiokol solid rocket engine. In Production. Delta-V reentry motor developed as a spin-up and propulsion motor for reentry vehicles. The design incorporated an aluminum case and a plastic nozzle assembly. |
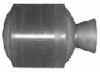 | Star 75 Thiokol solid rocket engine. In Production. A demonstration motor tested as a first step in the development of a perigee kick motor in the 4080-7940 kg propellant range. |
| Stonechat Mk 2 Royal Ordnance solid rocket engine. Out of production. There seem to have been even larger classified versions. Used on Falstaff launch vehicle. |
| Stonechat-1 RO solid rocket engine. Largest solid rocket motor ever produced in Britain. Motor developed for hypersonic research vehicle. Subsequently used in Falstaff test vehicle. Stonechat I first stage. |
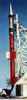 | Stromboli The second series of Sud Aviation sounding rockets were deployed in the late 1960's. They were designed to carry large diameter payloads, and used Stromboli motors only. |
| T-40 Thiokol solid rocket engine. Double Cajun T40 second stage. |
| T-55 Thiokol JATO solid rocket engine. HJ Nike Nike Recruit T55 fifth stage. |
| T-7 LRE SIMED/Shanghai solid rocket engine. T-7/GF-01A first stage. |
| T-7A Booster Fourth Academy solid rocket engine. T-7 sounding rocket. Out of Production. China's first flight solid rocket. First flight 1965. Polysulfide binder with aluminum binder fuel in case of high strength steel with a graphite throat insert. |
| Talos Mk 11 Mod 2 Hercules solid rocket engine. Talos motor fitted with a conical adapter for mating to the second stage. Solid propellant rocket stage. The Talos motor was fitted with a conical adapter for mating to the second stage. Differential drag forces caused separation. Four fins were arranged at the aft end in a cruciform configuration and drove the vehicle to approximately one revolution per second burnout roll rate. Talos first stage. |
| TE-307 Thiokol solid rocket engine. Paiute Apache second stage. |
| TE-388 Thiokol solid rocket engine. Nike Iroquois second stage. |
| TE-416 Thiokol solid rocket engine. |
| TE-473 Thiokol solid rocket engine. Sandhawk Tomahawk first stage. |
| Terrier ASAS-2 Solid propellant rocket stage. Second stage of Terrier ASAS sounding rocket. |
| Terrier Mk12 Mod 0 Naval Prop Plant solid rocket engine. The Terrier MK 12 Mod 1 rocket motor was typically equipped with four 0.22 square meter fin panels arranged in a cruciform configuration. Solid propellant rocket stage. The Terrier MK 12 Mod 1 rocket motor was typically equipped with four 0.22 square meter fin panels arranged in a cruciform configuration. |
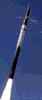 | THAAD American anti-ballistic missile. Theatre High-Altitude Air Defense. SDIO/BMDO project. Single stage vehicle. |
| Theodore ATEF solid rocket engine. Monica I second stage. |
| Thiokol 156 Thiokol solid rocket engine. Developed to 1966. |
| Tiny Tim Test vehicle using a Naval Propellant Plant solid rocket engine. |
| TKS SAS Russian manned spacecraft module. 4 launches, 1977.07.17 (Cosmos 929) to 1985.09.27 (Cosmos 1686). Emergency escape system. |
| TR-1-1 Solid rocket stage. 608.00 kN (136,684 lbf) thrust. Mass 10,800 kg (23,810 lb). |
| TR-1A-1 Solid rocket stage. 608.00 kN (136,684 lbf) thrust. Mass 7,500 kg (16,535 lb). |
| Tramontane SEPR solid rocket engine. Out of production. Used on Berenice launch vehicle. First flight 1962. Berenice third stage. |
| Trident Motor Philco-Ford solid rocket engine. Atlas F/Trident second stage. |
| Trident St 3 CSD solid rocket engine. Trident D-5, Trident C-4 third stage. |
| TT-500-S2 NASDA solid rocket engine. TT-500 second stage. |
| TU-715 Thiokol solid rocket engine. Ute Tomahawk first stage. |
| TU-716 Thiokol solid rocket engine. Paiute Apache first stage. |
| TU-758 Thiokol solid rocket engine. Terrier Malemute second stage. |
| TU-904 Thiokol solid rocket engine. Peacekeeper first stage. |
| TX-135 Thiokol solid rocket engine. Nike Zeus first stage. |
| TX-174 Thiokol solid rocket engine. Pershing 1A first stage. |
| TX-175 Thiokol solid rocket engine. Pershing 1A second stage. |
| TX-20 Thiokol solid rocket engine. Draco first stage. |
| TX-238 Thiokol solid rocket engine. Nike Zeus second stage. |
| TX-239 Thiokol solid rocket engine. Nike Zeus 3 third stage. |
| TX-30 Thiokol solid rocket engine. Draco second stage. |
| TX-33 Thiokol solid rocket engine. Polaris TV first stage. |
| TX-454 Thiokol solid rocket engine. Spartan ABM second stage. |
| TX-500 Thiokol solid rocket engine. Spartan ABM first stage. |
| TX-52 Thiokol solid rocket engine. Doorknob 1 first stage. |
| TX-664-4 Thiokol solid rocket engine. Basic Terrier mk70 motor. Solid propellant rocket stage. Thrust kN. The basic Terrier mk70 motor was 3.94 m long with a principal diameter of 46 cm. There was a 7.6-cm interstage adapter which allowed for drag separation at Terrier burnout. Typically, the Terrier booster would utilize two spin motors to reduce dispersion and also serve as drag plates. Each Terrier fin was 0.43 square meters in area. Normally, the fins were canted to provide two revolutions per second spin rate at Terrier burnout. Terrier Mk 70 Oriole first stage. |
| TX-77 Thiokol solid rocket engine. Castor Lance second stage. |
| UA1205 CSD solid rocket engine. Out of production. Strap-on boosters for Titan 3C, 3D, 3E. Proposed for advanced Saturn IB versions. First flight 1965. |
| UA1206 CSD solid rocket engine. Used on Titan 34D launch vehicle. First flight 1982. |
| UA1207 CSD seven-segment solid rocket engine, originally developed in the 1960's for the cancelled MOL project. First flight 1989. |
| UA-156 CSD solid rocket engine. Tested 1968. Proposed as strap-on booster for Saturn INT-27, Saturn V-25(S)B, Saturn V-25(S)U. Solid propellant rocket stage. 4 Segment version of basic 3-segment UA 156 motor. |
| UM-129A Nissan solid rocket engine. In Production. Used in H-1-3. |
| USRM Hercules solid rocket engine.Strap-on booster for Titan 4B. First flight 1997. |
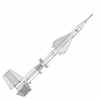 | V-1000 Russian anti-ballistic missile. First Soviet anti-ballistic missile system. Development began in 1956 and the system was tested at Sary Shagan 1960 to 1961. It was clear that enormous development work was needed to achieve an operational anti-ballistic missile system. Therefore work began on the successor A-35 system, although the Americans were led to believe that an operational system was deployed around Moscow. The System A anti-ballistic missile equipped with the V-1000 rocket made the first intercept and destruction in the world using a conventional warhead of an intermediate range ballistic missile warhead coming in at 3 km/s on 4 May 1961. The US did not demonstrate an equivalent capability until 1984. |
| Vega engine Sud solid rocket engine. Belier III first stage. |
| Vela engine WRE solid rocket engine. Aero High second stage. |
| Venus engine Sud solid rocket engine. Centaure 2C first stage. |
| Vero P2 LRBA solid rocket engine. Veronique P2 first stage. |
| Vero P6 LRBA solid rocket engine. Veronique P6 first stage. |
| Veronique R French sounding test vehicle. 'Veronique Reduce' - test vehicle for the full-size Veronique, with the burn time of the engine limited to 6.5 sec instead of the nominal 32 sec. Tested in France at the Suippes range in 1950 and 1951, then at Cardonnet in early 1952. |
| Viper-20 Multiple-source American solid rocket engine. Viper Viper-Dart first stage. |
| Viper-25 Aerojet solid rocket engine. Viper 3A first stage. |
| Viper-27 Multiple-source American solid rocket engine. |
| Voskhod KDU Russian manned spacecraft module. Study 1965. Auxiliary Retrorocket. |
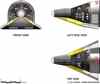 | Winged Gemini American manned spaceplane. Study 1966. Winged Gemini was the most radical modification of the basic Gemini reentry module ever considered. |
| X-220 Hercules solid rocket engine. Double HPAG Deacon second stage. |
| X-241 Hercules solid rocket engine. Project Pilot 1 third stage. |
| X-250 Hercules solid rocket engine. Polaris A2E, Polaris A2 second stage. |
| X-256 Hercules solid rocket engine. Black Brant X first stage. |
| X-260 Hercules solid rocket engine. STARS second stage. |
| X-265 Hercules solid rocket engine. Sprint ABM first stage. |
| X-271 Hercules solid rocket engine. Sprint ABM second stage. |
| XM-42 Hercules solid rocket engine. Nike Hercules first stage. |
| XM-45 Rocket solid engine. Trailblazer 2 M second stage. |
| Yardbird Thiokol solid rocket engine. Nike Yardbird second stage. |
| Zefiro FiatAvio solid rocket engine. Scout II TV first stage. |
| Zefiro 23 Fiat-Avio solid rocket engine. In production. Carbon epoxy filament wound case; low density EPDM insulation; HTPB 1912 composite propellant. Used on Vega launch vehicle. Solid propellant rocket stage. The Zefiro 23 was derived from a 16-metric ton solid rocket motor development (Zefiro 16) initiated by Fiat-Avio, now Avio S.p.A., with company funding and contracted by the Italian space agency ASI. |
| Zefiro 9 Fiat-Avio solid rocket engine. In production. Motor derived from the 16-metric-ton Zefiro 16. Carbon epoxy filament wound case; low density EPDM insulation; HTPB 1912 composite propellant. Solid propellant rocket stage. The Zefiro 9 was derived from a 16-metric ton solid rocket motor development (Zefiro 16) initiated by Fiat-Avio, now Avio S.p.A., with company funding and contracted by the Italian space agency ASI. |
| Zenit C Oerlikon solid rocket engine. Zenit C first stage. |
| Zeus A GCR solid rocket engine. Nike Zeus A second stage. |
| ZIF-IR-189 Solid propellant rocket stage. . Used monolithic single motor with Nylon-S propellant. Combustion chamber pressure 30-40 kg/cm2. |
| ZIF-IR-190 Solid propellant rocket stage. . Used cluster of four motors with Nylon-B propellant. |
| ZIF-IR-191 Solid propellant rocket stage. . Used cluster of four motors with Nylon-B propellant. |
| ZIF-IR-194 Solid propellant rocket stage. . Used monolithic single motor with Nylon-S propellant. |
| ZN-1 NUDT Changsha solid rocket engine. Zhinui first stage. |
Engines: Ajax engine,
Aerobee 100 engine,
Improved Orion engine,
LR2-RM-6,
SPT-100-SEP,
SPT-100,
SR105,
SR109,
SR11,
SR113,
SR114,
SR115,
SR116,
SR121,
SR122,
SR13,
SR45,
SR49,
SR51,
SR55,
SR59,
SR61,
SR75,
SR9.
Spacecraft: LL,
Gemini AM,
Mercury,
Mercury Retropack,
Paracone,
Dynasoar AS,
Gemini Ferry AM,
Voskhod KDU,
MOL,
GE Life Raft,
Lockheed EEOED,
Winged Gemini,
Gemini B AM,
MOL LM,
ENCAP,
Shuguang 1,
EGRESS,
FSW,
Apollo CM Escape Concept,
Northrop LBEC,
TKS SAS,
DFH-2,
Alpha Lifeboat,
Contour,
Orion LAS.
Launch Vehicles: HVAR,
FFAR,
Veronique R,
Rockair,
K150,
V-1000,
Loki,
Nova 5S,
MR-12,
Meteor-1,
MT-135,
Sirocco,
S-160,
BT-310,
S-210,
RH-75,
NAL-7,
MMR-06,
RH-125,
Meteor-2K,
MLRS,
S-310,
RH-200,
53T6,
S-520,
Atlas E/SGS-2,
RX-250-LPN,
DF-15,
DF-11,
Excalibur,
THAAD,
Excalibur Target System,
SR19/SR19,
KT-1,
GoFast,
SpaceLoft,
SpaceLoft XL,
Icarus.
Stages: Vero P2,
Vero P6,
Veronique R-1,
HPAG engine,
Mk7,
3-DS-47000,
NOTS 124-C,
Kappa 1 engine,
Oreste,
Theodore,
Kappa 4 Booster,
Kappa 4 engine,
K245-1,
TX-33,
Kappa 5-1,
Arcon booster,
Arcon-1,
Asp II engine,
Cygnus 20,
TX-20,
TX-30,
TX-52,
Neptune engine,
SEPR 685-4,
200 inch solid segment x 4,
200 inch solid segment x 6,
5.6KS5400,
MB-1 engine,
Zeus A,
Rook engine,
Hopi 3.0KS4000,
Hopi 2.4KS5600,
Hopi 9.0KS1800,
Cirrus I engine,
Cirrus II engine,
Kisha I 4.4KS4800,
LAPSTAR-300,
SPRAN-50,
Kappa 9L-1,
Belier II engine,
Vega engine,
Algol 1,
Altair 1,
Cuckoo IB,
Kartukov Soyuz SAS,
SEPR 740,
Tramontane,
Melanie,
Kappa 9M-2,
Deacon Arrow II-2,
Judi-III 1.9KS2100,
Kiva 5.5KS6100,
Lambda 2-2,
Martlet 3-1,
Meteo-1,
RM-1100,
RM-1400,
S-A engine,
Seliger 1 engine,
Seliger 3 engine,
SEPR P163,
SEPR P191,
X-220,
Altair 1A,
Mk 36,
23KS20000,
A1P-1,
A1P-2,
AJ-260-1/3,
AJ-260-2,
AJ-260X 1/3,
Algol 2,
Cuckoo II,
Gamma Centauro-1,
Gamma Centauro-2,
HM-16 engine,
K10S,
Lambda 3-2,
Lambda 3-3,
LS-A engine,
RD RT-15-2,
Squirt-1,
ST engine,
Orion engine,
Algol 1D,
HARP-1,
HIBEX engine,
K160,
K250H,
LAPSTAR-52,
M55A1,
Martlet 2-1,
Martlet 2G1-1,
Martlet 2G1-2,
Martlet 4-1,
Martlet 4-2,
Martlet 4-3,
Mayfly-300,
Orion-1 engine,
Pollux,
Sonda 1 Booster,
Sonda 1 engine,
TX-238,
TE-473,
5D22,
5S47,
AJ-260X,
MT 27,
NA801,
MARC 13A1,
MARC 14B1,
SA-II engine,
Belisama engine,
15D23P,
15D24P,
15D94,
Agnes,
Emilie,
Melusine,
NAL-16 engine,
NAL-25 engine,
S-C engine,
SO-250,
Stonechat-1,
T-7 booster,
T-7 LRE,
X-250,
Antares 1A,
K250-8,
MR-25 engine,
A2P-1,
Algol 2B,
MARC 42A1,
S-B engine,
Altair 3D,
Judi-I 1.9KS2150,
M-20,
MARC 14A1,
SEPR 739-2,
SEPR P167,
SNP Jericho,
Upstage engine,
SPT-50,
Altair 2,
Cygnus 15,
Orion-2 engine,
1.8KS7800,
15D27,
23KS11000,
Gosling 4,
JCR engine,
LS-C-2.5,
LS-C-4,
Alcor 1B,
MARC 2C2,
Mk 17,
TX-239,
Cajun,
TT-210 engine,
TU-715,
15D305,
15D339,
L500,
L735,
L735(1/3),
RH-125S,
SEP 903,
Javelin 3 engine,
Canopus,
Kartukov Soyuz T - TM SAS 17k,
Kartukov Soyuz T - TM SAS 73k,
Astrobee D engine,
K420(1/3),
SEP 904,
Star 37XE,
Nihka,
Bantam 2,
Bantam 3,
TU-716,
Venus engine,
SPT-70,
Astrobee F engine,
SLV-3 engine,
TT-500 engine,
TT-500-S2,
Ariane 3-0 P7.35,
9KS11000,
M-22,
M-3A,
SB-310,
Ariane 4-0 P9.5 SPB,
12KS10000,
TX-77,
K420H,
M-6,
Pershing 2 St1,
Pershing 2 St2,
RD RT-21-3,
UA1207,
Perigee Orbit Transfer Motor,
Cuckoo IA,
Cuckoo 4,
Goldfinch IIA,
MARC 2B1,
MARC 60A,
MR-20 engine,
RD RT-21 (1),
RD RT-21-2,
SICBM-1,
H-1-3,
UA1206,
X-265,
Algol 3,
M-100-100,
M-100-300,
Mage 2,
RH-300 engine,
Rita II,
ST-735-1,
ST-735-2,
Antares 2,
M-13,
M-23-Mu,
SB-735 engine,
RSRM,
Ariane 5-0 P230,
S-30 engine,
1.5KS35000,
RH-560 engine,
TR-1-1,
TR-1A-1,
15KS25000,
M57A1,
Rocketsonde-1,
Ariane 5-0 P241,
TU-904,
100 inch solid,
15D151,
15D169,
15D206,
15D23,
15D24,
15D25,
15Zh58A,
15Zh58B,
15Zh58V,
160 inch solid,
26KS20000,
2.5KS18000,
22.6KS1245,
240 inch solid,
280 inch solid,
293-P,
300 inch solid,
325 in solid,
51T6 Motor,
9KS1660,
A3P-1,
Agni St2,
Agni3 S2,
Agni 3 engine,
Altair 3,
Antares 3,
Algol 3A,
Altair 3A,
Antares 3A,
Altair 3B,
Algol 2C,
Agni engine,
ABL Snark JATO,
Acheron,
Aerojet SRB,
Alcor,
Alfa engine,
ASROC,
Aurore,
Burner 2A,
Bantam,
BB7,
BE-3,
BE-3B1,
Black Arrow-3,
Bullpup,
Castor 1,
C4-2,
Castor 2,
CZ-1D-3,
Castor 4A engine,
Castor 4AXL H-2A,
Castor 4B engine,
Castor 4AXL,
Castor 4BXL,
Castor 4XL,
C3-1,
C3-2,
C4-1,
Castor 120,
Castor 4,
Chick,
Cygnus 5,
DF-21-1,
DF-21-2,
D-5-1,
D-5-2,
DAC Roc-1,
Demon,
DFH-2 AKM,
DP Boost,
DS engine,
Dushkin 3M9,
EPKM,
Falcon engine,
FFK,
FSW Retromotor,
GEM 40,
GEM 60,
GEM 46,
Goldfinch II,
GCRC,
GF-02,
Goldfinch,
Goose II,
Gosling,
Shuttle ASRM engine,
H-2/J-1-1,
H-2-0,
HOTROC,
Hydac,
Hyperion-1,
IAI-Arrow-2-1500,
IAI-Arrow-2-500,
Icarus St2,
IAI-Arrow-1,
Iris engine,
Jupiter C-2,
Juno II-3,
Jericho II engine,
K250-100,
K250-200,
K250-300,
K420-1200,
K420-1400,
K420-1800,
K420-500,
Kartukov P-15M,
K220,
Kartukov LL,
Kartukov P-35,
Kartukov P-5,
Kartukov P-6,
KM-D,
KM-H,
KSR-1,
L480S,
Lapwing,
LK-1 engine,
Lobster,
LPC A-1,
LPC-415,
LS-A Booster,
Lupus,
Lynx,
M5E1,
Mage 1,
MIHT-1,
MSBS 501,
M55/TX-55/Tu-122,
MIHT-2,
MSBS 502,
MIHT-3,
MSBS 503,
M24,
M-V-4,
Martlet 3E stage,
M-23-J,
M-3B-J,
M-3B-Mu,
M-10,
M-30,
M-40,
M14,
M34,
M56A-1,
Mammouth,
Mayfly-600,
MG-18,
MIHT-4,
Mk 104,
Mk 30,
Mk 39,
Mk 72,
MR-125,
Musca,
NAL-735 engine,
NOTS 100A,
NOTS 3SM,
NOTS 401A,
NOTS 8,
NOTS Mod 551-B,
NOTS-1,
NOTS-3,
NOTS-4,
NSPO Booster,
NSPO Sustainer,
Orion 50SXLG,
Orbus 1,
Oriole,
Peacekeeper 1,
Pegasus XL-1,
Pegasus-1,
Pegasus XL-2,
Pegasus-2,
Pegasus-3,
Prithvi engine,
P4,
P6,
P80,
PRD-15,
PRD-19M,
PRD-22,
PRD-33,
PRD-36,
PRD-52,
PRD-61,
PRD-70,
PSLV-1,
PSLV-3,
RTV-100,
RTV-500,
RH-300-II,
Redesigned SRM,
R-31 RV Bus,
R-31 Stage 1,
R-31 Stage 2,
Raven 1,
Raven 11,
Raven 2,
Raven 5,
Raven 6,
Raven 7,
Raven 8,
RD RT-1-3,
RD-127,
RM-3141,
RSA-3-1,
RSA-3-2,
RSA-3-3,
RSA-4-1,
RSA-4-2,
RT-2-1,
Castor engine,
Super Loki engine,
SPT-140,
SPT-200,
SPT-290,
SS-520 engine,
S-31,
SEP 401,
SEP 402,
S-23,
S-43,
SEP 403,
Soleil NA803,
Strela-3 stage,
S-44,
Star 37XF 8,
Star 48 8,
SRB-A,
Star 12A,
Star 13A,
Star 17A,
Star 24A,
Star 27A,
Star 30A,
Star 5A,
Star 6A,
Star 13B,
Star 24B,
Star 26B,
Star 27B,
Star 30B,
Star 37B,
Star 48B,
Star 5C/CB,
Star 5CB,
Star 6B,
Star 13C,
Star 24C,
Star 26C,
Star 27C,
Star 30C,
Star 37C,
Star 5C,
Star 13D,
Star 27D,
Star 37D,
Star 63D,
Star 13E,
Star 27E,
Star 30E,
Star 37E,
Star 13F,
Star 37F,
Star 37XF,
Star 63F,
Star 37G,
S-40TM,
S-43TM,
Star 37FM,
Star 37N,
Star 30BP,
Star 37XFP,
Star 37S,
Star 48V,
Star 37X,
Star 37Y,
Soleil Mammouth,
Star 20 Spherical,
Star 48A l,
Star 48B l,
Star 48A s,
Star 48B s,
S-20,
S-300 engine,
Seagull-1,
SEP 901,
SEP 902,
SEPR 734-1,
SEPR 737,
SEPR 740-3,
SEPR-732,
SICBM2,
SICBM3,
SICBM4,
Skybolt,
Skybolt 2,
SLS SRB 2720,
SLS SRB 388,
SLV-1,
SLV-2,
SLV-4,
SM3 TSRM,
Snipe,
SpaB-54,
Sparrow,
SPRD-15,
SPRD-30,
SPRD-99,
SR19,
SR110,
SR119,
SR120,
SR71,
SR73,
SRB,
SRM-1,
SRM-2,
SSUS-A Motor,
Star 10,
Star 12,
Star 13,
Star 15,
Star 17,
Star 24,
Star 25,
Star 26,
Star 27,
Star 30,
Star 37,
Star 40,
Star 48,
Star 5,
Star 6,
Star 62,
Star 63,
Star 75,
Stonechat II,
Stonechat Mk 2,
Stromboli,
TR-1-10800,
TR-1-7500,
TT-200 engine,
Terrier Mk12 Mod 1,
TU-758,
Taurus engine,
T-40,
T-55,
T-7A Booster,
Taepodong 1-3,
Talos Mk 11 Mod 2,
TE-307,
TE-388,
TE-416,
Terrier ASAS-2,
Terrier Mk12 Mod 0,
Thiokol 156,
Tiny Tim,
Trident Motor,
Trident St 3,
TX-135,
TX-174,
TX-175,
TX-261-3,
TX-454,
TX-500,
TX-664-4,
UA1205,
UM-129A,
UA-156,
USRM,
Viper-20,
Viper-25,
Viper-27,
Vela engine,
X-260,
X-241,
X-256,
X-271,
XM-42,
XM-45,
Yardbird,
Zefiro 23,
Zefiro 9,
Zefiro,
Zenit C,
ZIF-IR-189,
ZIF-IR-190,
ZIF-IR-191,
ZIF-IR-194,
ZN-1.
Back to top of page
Home - Search - Browse - Alphabetic Index: 0- 1- 2- 3- 4- 5- 6- 7- 8- 9
A- B- C- D- E- F- G- H- I- J- K- L- M- N- O- P- Q- R- S- T- U- V- W- X- Y- Z
© 1997-2019 Mark Wade - Contact
© / Conditions for Use