Home - Search - Browse - Alphabetic Index: 0- 1- 2- 3- 4- 5- 6- 7- 8- 9
A- B- C- D- E- F- G- H- I- J- K- L- M- N- O- P- Q- R- S- T- U- V- W- X- Y- Z
CEV Andrews
Part of Orion CEV
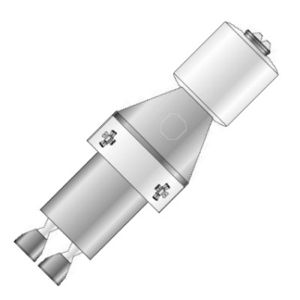 CEV Andrews Credit: © Mark Wade |
American manned spacecraft. Study 2005. The Andrews Crew Exploration Vehicle (CEV) design adopted NASA's preferred Apollo CM re-entry vehicle shape, but combined it with a mission module crew cabin to minimize the CEV's mass.
Status: Study 2005. Gross mass: 21,057 kg (46,422 lb). Height: 10.00 m (32.00 ft). Diameter: 4.50 m (14.70 ft).
Andrews' CEV concept was an Apollo-type re-entry module, used together with a forward cylindrical mission module, an aft orbital transfer vehicle for propulsion, and a launch escape system abort tower. The capsule, while only 4.5 m in diameter, would meet NASA's objective of allowing return of four crew normally, and six in the role of a space station life boat or ferry. The CEV would be capable of unmanned remote operation, including rendezvous and docking, in order to serve as a rescue vehicle, a payload delivery/return vehicle, or to dock with an LSAM lunar lander. For lunar missions, a standard orbital transfer vehicle (OTV) would be used; for lifeboat missions a more modest 4.5-m-diameter Service Module would be used.
For the lunar mission, Andrews envisioned using an L1 way station and an elaborate infrastructure of vehicles. These vehicles would be proven in lunar exploration and then used later for Mars expeditions. The L1 way station was considered to have overriding operational advantages in terms of global access, launch anytime from earth or the moon to reach it. However this came at an enormous cost, with nearly $100 billion required to put the first lunar base on the surface. For the first lunar mission, a crew of four would spend ten days on the surface. This would then be expanded into an eight-member lunar base, with tours of duty of up to a year. To accomplish all this the following vehicles were proposed:
- An expendable booster for the Earth to Orbit (ETO) Segment, which would consist of two lateral Zenit-2 boosters and an Atlas V Core stage, topped by a Lox/LH2 Expendable Upper Stage (EUS). This Expendable Common Booster (ECB) could deliver a 22,000 kg CEV to translunar injection or 40,000 kg of cargo to low earth orbit within a 5 x 2 0m fairing. Development cost was not estimated. Cost per launch would be $240 million.
- A reusable Crew Exploration Vehicle (CEV) to take crews to the L1 Transfer Hub and return them to earth. It would be powered by an OTV (orbital transfer vehicle) stage.
- A reusable LEO-L1 Tug (LLT) that would deliver 63,000 kg from LEO to L1 and return 15,000 kg from L1 to LEO. It would have a stowed envelope of 5 x 10m, and be powered by a solar electric (Hall or ion) engine using xenon propellant. Propellant for a particular mission would be launched with the mission payload to low earth orbit. The tug would then rendezvous with the payload, and use the propellant to take the payload to L1. The tug would be equipped with a 300 kW solar power array, using solar concentrators to reduce cost, and a manipulator arm for payload berthing. A transfer mission would take 180 days taking advantage of n-body trajectory flybys of the moon and earth, or 320 days using conventional orbital mechanics. Critical technology that would have to be developed included 100+ kW electric thrusters, highly packageable solar array / concentrators, and low-cost hardened solar cells, The LLT's SEP propulsion unit would have an ideal delta-V of 3.4 km/s, a mass of 4,456 kg, a specific impulse of 3850 seconds, and a thrust of 11.9 N. Development cost would be $6.318 billion, with first unit cost being $223 million and an annual operating cost of $13.7 million. The tug would rendezvous with a payload and propellant combination with a total mass of 91,452 kg. Of this, 78,284 kg would be payload, and 12,260 kg propellant and propellant tankage. Much of the payload delivered to L1 would be water, which would be converted to liquid hydrogen and oxygen there, and used for rocket propellant.
- A reusable L1 Transfer Hub (LTH) which would provide in-transit support for up to eight crew for stays of five days at a time during crew rotation; for eight crew up to three days in the storm shelter in case of a solar storm; or a crew of four for 14 days for housekeeping of the transfer hub. The LTH would have docking ports for 2 CEV's, 2 CPL Landers, and extensible logistics modules. Up to 18 water tanks could be attached. Total development cost would be $27.095 billion, with the LTH costing $1.670 billion to fabricate and having an operating cost per mission of $92.7 million. Subelements of the LTH and other free-flying unmanned elements of the lunar exploration infrastructure in other lunar orbits would include:
- Lunar Reconnaissance Orbiter (LRO)
- Lunar Science Rover (LSR)
- Farside Communications Node (FCN)
- Tug Propellant Module (TPM)
- Modular Water Tank (MWT)
- Station Utility Module (SUM)
- Space Habitation Module (SHM)
- Interconnect Module (ICM)
- A reusable Common Planetary Lander (CPL) that would deliver 15 metric tons of cargo from L1 to the lunar surface on a one-way mission, or a 5.4 metric ton manned module from L1 to the lunar surface and back to L1. It would accommodate underslung 5 x 10 m Payload Modules, and be powered by two RL-10 LOX/LH2 main engines. Reaction control would be via a GOX/GH2 thruster system. Propellant for the lander initially be electrolysised from water delivered from earth to the LTH depot. Later it would come from water generated from a lunar ISRU plant. Critical technology that needed to be developed included the GOX/GH2 ACS thrusters; long duration / low boil-off cryogenic tanks; and automatic lunar landing guidance and control technology. Development cost of the CPL would be $ 3.694 billion, with the first unit costing $ 253 million and each mission having an operations cost of $ 18.5 million. Mass breakdown of the CPL would be:
- Launch Mass: 56,845 kg
- Payload: 15,000 kg
- Propellant / Fluids: 33,300 kg
- Dry Mass: 8,545 kg
- Margin: 1,115 kg
- Equipment: 970 kg
- Propulsion: 1,690 kg
- Structure/Thermal: 4,770 kg
Modules of the CPL would include:
- Crew Transfer Module (CTM)
- Pressurized Cargo Carrier (PCC)
- Unpressurized Cargo Carrier (UCC)
- A reusable Lunar Surface Node (LSN) that would support four crew for six-month tours of duty on the lunar surface. Each person would have over 30 cubic meters of living volume. One module of the node would be buried in regolith to provide a radiation shelter during solar storms. The modular outpost would be built up of 15 metric ton elements delivered to the surface by the CPL. Eventually a water based ISRU capability from would be introduced at a separate plant, producing water from lunar ice or lemnite ore. Liquid hydrogen and oxygen would be manufactured from the water for use as propellants. A
rover tanker module would be used for propellant transport. Development cost would be $14.051 billion; hardware cost $ 1.041 billion; and annual operating cost $ 115.0 million. Mass breakdown for 15-metric ton individual modules would be:
- Inflatable Module: 1,541 kg
- Equipment in ECLSS: 3,172 kg
- EMU (EVA Suit Spares): 204 kg
- Structure: 6,184 kg
- Crew Systems: 786 kg
- Work Stations: 486 kg
- Logistics: 1,010 kg
- ECLSS: 1,716 kg
Other elements of the lunar base and its support would include:
- Human Exploration Rover (HER)
- Surface Power Module (SPM)
- Long Duration Habitat (LDH)
- Mobile ISRU Plant (MIP)
Development Cost $: 6,456.000 million. Unit Cost $: 284.000 million. Cost Notes: First unit cost; 2005$; ops cost $62.1 mn/mission.. Crew Size: 6. Habitable Volume: 12.00 m3.
Family:
Lunar Bases,
Manned spacecraft,
Moon.
Country:
USA.
Spacecraft:
CEV Andrews MM,
CEV Andrews OTV,
CEV Andrews RM.
Launch Vehicles:
Andrews ETOS.
Agency:
NASA,
Andrews.
Photo Gallery
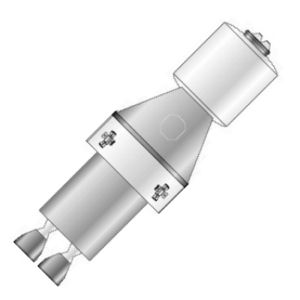 | CEV Andrews Credit: Mark Wade |
Back to top of page
Home - Search - Browse - Alphabetic Index: 0- 1- 2- 3- 4- 5- 6- 7- 8- 9
A- B- C- D- E- F- G- H- I- J- K- L- M- N- O- P- Q- R- S- T- U- V- W- X- Y- Z
© 1997-2019 Mark Wade - Contact
© / Conditions for Use