Home - Search - Browse - Alphabetic Index: 0- 1- 2- 3- 4- 5- 6- 7- 8- 9
A- B- C- D- E- F- G- H- I- J- K- L- M- N- O- P- Q- R- S- T- U- V- W- X- Y- Z
Shenzhou SM
Part of Shenzhou
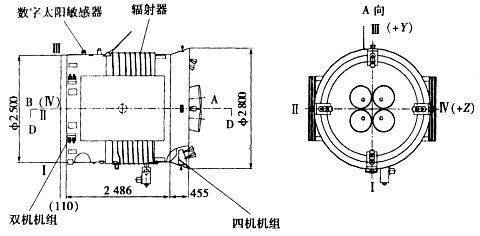
Shenzhou
Shenzou SM Dimensioned Drawing
Chinese manned spacecraft module. Operational, first launch 1999.11.19. The service module, developed by the Shanghai Academy of Space Technology, provides the electrical power, attitude, control and propulsion for the spacecraft in orbit.
Status: Operational 1999. Thrust: 10.00 kN (2,248 lbf). Gross mass: 3,000 kg (6,600 lb). Unfuelled mass: 2,000 kg (4,400 lb). Specific impulse: 290 s. Height: 2.94 m (9.65 ft). Diameter: 2.50 m (8.20 ft). Span: 17.00 m (55.00 ft).
It was the same form as that of Soyuz, but longer, fatter, and the flared base was less pronounced. As on Soyuz, the bottom portion of the module was used as an external radiator surface for the spacecraft's thermal regulation system. Two solar panels, with a total span of over 17 m, deployed from the sides of the service module. Unlike those of Soyuz, these could be rotated to obtain maximum solar insolation regardless of spacecraft attitude. Roll and translation attitude control engines were arranged at the forward end of the service module. Within the flared base of the module a unique arrangement of thrusters (firing from the outer rim of the flared base toward the central axis of the spacecraft) controlled pitch and y
Within the service module there were several ellipsoid-shaped compartments that housed avionics, electrical, and environmental control system equipment. Also located in the service module were the nitrogen and oxygen gases for the environmental control system. These were stored in steel alloy spheres at a pressure of 21 Mpa. To reject the 1 kW of heat generated by Shenzhou's crew and internal systems, a cooling system used heat pipes to conduct heat from internal systems to the external radiator.
Primary electrical was provided by the two solar panels, which had a total area of 24.48 square meters. Each panel was in four sections, which were folded during launch. The two panels on the orbital module were of two sections each, and provided an additional 12.24 square meters of panel area. The back surface filled silicon solar cells of the arrays had an efficiency of 14.8%. Sun sensors between the panels measured the sunlight incidence angle which allowed the panels to be automatically commanded to an optimum angle. Silver-zinc batteries in the service module could provide six hours of emergency power in case of failure of the solar arrays. The spacecraft's power bus operated at 28 V and a peak power of 3.5 kW.
The unified propulsion system of the service module fed both attitude control and main engines from four 230-litre propellant tanks loaded with 1,000 kg of N2O4/MMH propellants. The engines were pressure fed using six 20-litre titanium cold gas tanks pressurized to 23 Mpa. This gas was used to force propellant at 2 Mpa using diaphragms within the propellant tanks. The engines consisted of:
- Four large expansion ratio main engines at the base of the spacecraft, with a thrust of 2.5 kN each. Specific impulse was 290 seconds. Burn time at retrofire would be about 75 seconds.
- Eight 150-N high-thrust pitch and yaw thrusters arranged in four pairs on the inside of the flared based of the service module.
- Eight low-thrust 5-N pitch and yaw thrusters arranged in four pairs on the outside of the flared base. These could also, when used together, provide reverse thrust.
- Eight low-thrust 5-N roll / translation thrusters mounted four pairs at the spacecraft center of gravity, just below the re-entry capsule. These were not placed at ninety degree intervals but in two pairs at each side of the spacecraft, allowing use for translation in the vertical axis only.
During orbital flight four groups of four 5-N thrusters mounted at the base of the orbital module were also available. This separate system used hydrazine monopropellant, pressure-fed at 23 Mpa from a 7-litre titanium cold gas tank. They were primarily used for autonomous attitude control and maneuvering capability to the orbital module when in free flight after Shenzhou's manned mission was completed. However they also could provide a backup to the main orientation system on the service module. Used in conjunction with the canted low thrust pitch and yaw thrusters at the base of the service module they could also provide translation in both horizontal and vertical planes during docking operations.
Many, many thanks to Chen Lan for providing original Chinese-language source material for this project, and to WXJ for the translation.
RCS Coarse No x Thrust: 8 x 150 N. RCS Fine No x Thrust: 16 x 5 N. Electric System: 2.40 kWh. Electric System: 1.00 average kW.
Family:
Manned spacecraft module.
Country:
China.
Spacecraft:
Shenzhou.
Propellants:
N2O4/MMH.
Agency:
CASC,
SAST.
Bibliography:
1791,
424,
460.
Photo Gallery
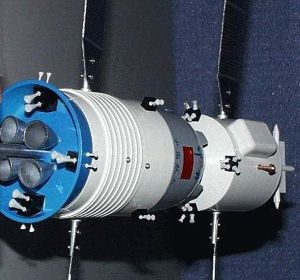 | Shenzhou Model Aft Unique view of the aft end of Shenzhou. The main propulsion system consists of four large expansion ratio main engines. Four groups of two large pitch / yaw thrusters are spaced around the inside of the flared service module skirt, with complementary groups of smaller thrusters mounted on the exterior of the skirt. The radiator loops of the service module wind around the module seven times (the same number as the early Soyuz 7K-OK design). The service module is 2.8 m in diameter at the flared base, 2.5 m in diameter over the radiator section, 2.4 m in diameter at the top, and 3.05 m in length (excluding the engines). This compares to 2.72 m base diameter, 2.15 m centre diameter, and 2.60 m length for the Soyuz. Credit: Steven S. Pietrobon |
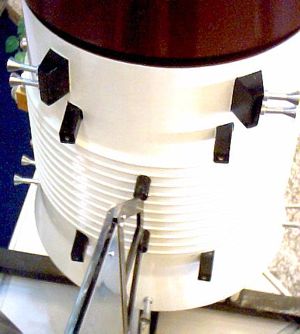 | Shenzhou Details Credit: © Mark Wade |
Back to top of page
Home - Search - Browse - Alphabetic Index: 0- 1- 2- 3- 4- 5- 6- 7- 8- 9
A- B- C- D- E- F- G- H- I- J- K- L- M- N- O- P- Q- R- S- T- U- V- W- X- Y- Z
© 1997-2019 Mark Wade - Contact
© / Conditions for Use